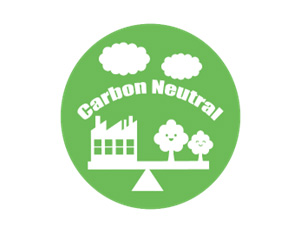
UBE Die Casting Machine Carbon Neutral Technology
UBE pursues ideal casting machine that meets the demands for high cycle rates in production process, lightweight components, and electrification, to contribute to carbon neutrality.
Click here to watch UBE Carbon Neutral TechnologyShot Unit Suitable for Making Structural Components: Extreme Shot
Concept
- ①Molten Metal Quick Filling : increases shot speed
- ②Beats filling resistance inside die - No stalling in shot process : intensifies filling force
- ③Reaches a target speed in a moment : Ramping up at a high speed
⇒ Intensifies shot speed and filling force in well balanced condition
Expands margin in a range of target shot speed
-
PQ2 line (Machine line)
-
Shot Capacity Upgrade
Extreme Shot Machine PQ2 Diagram
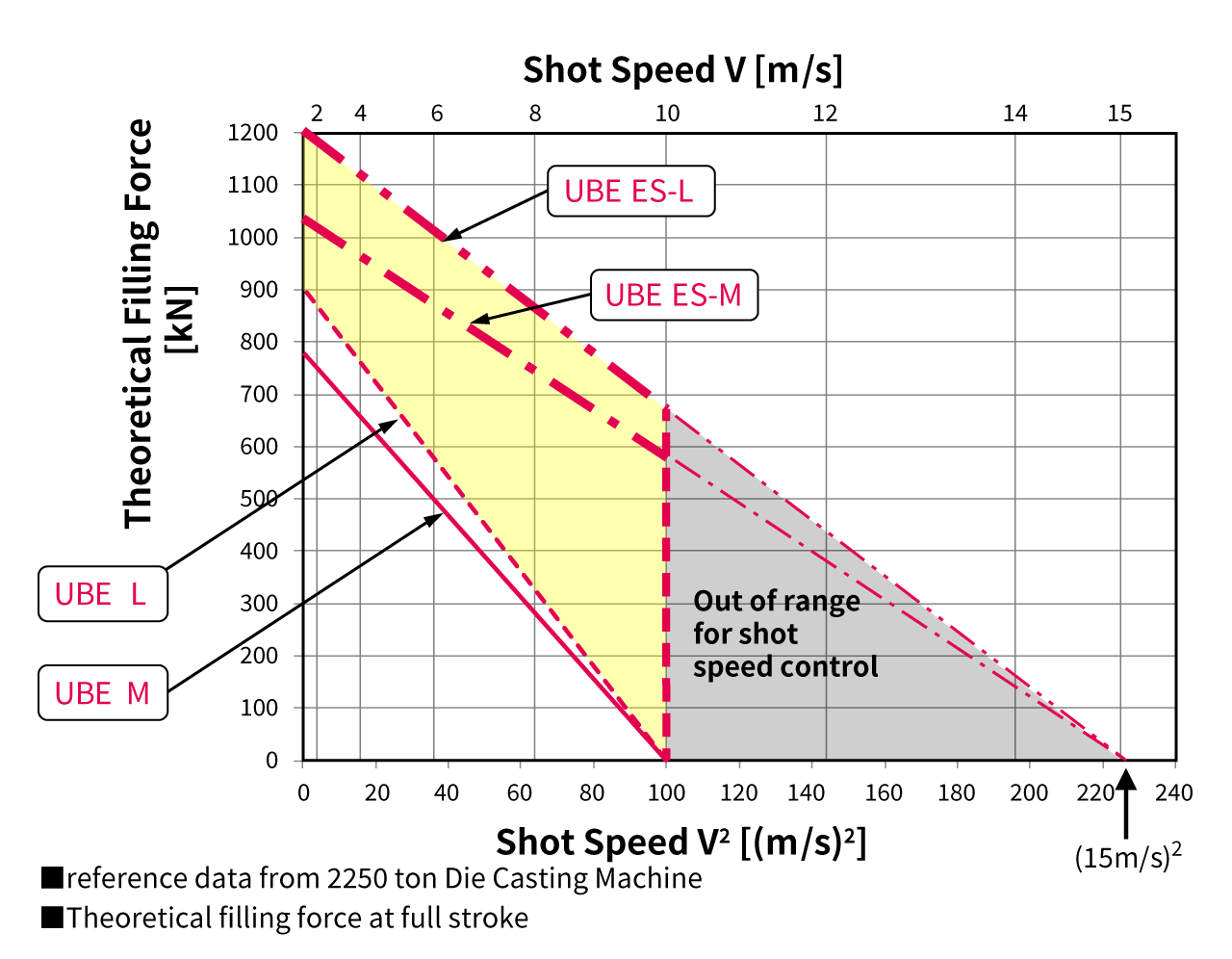
Extreme Shot Test Result
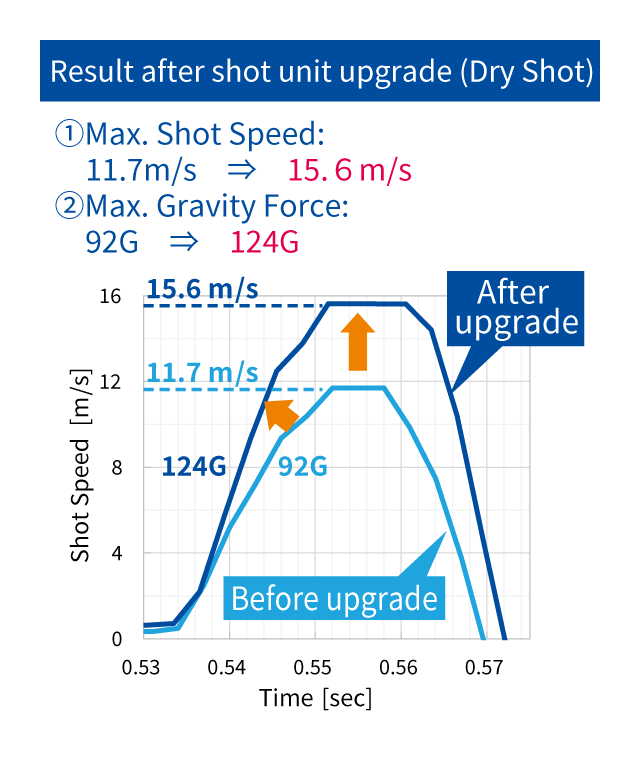
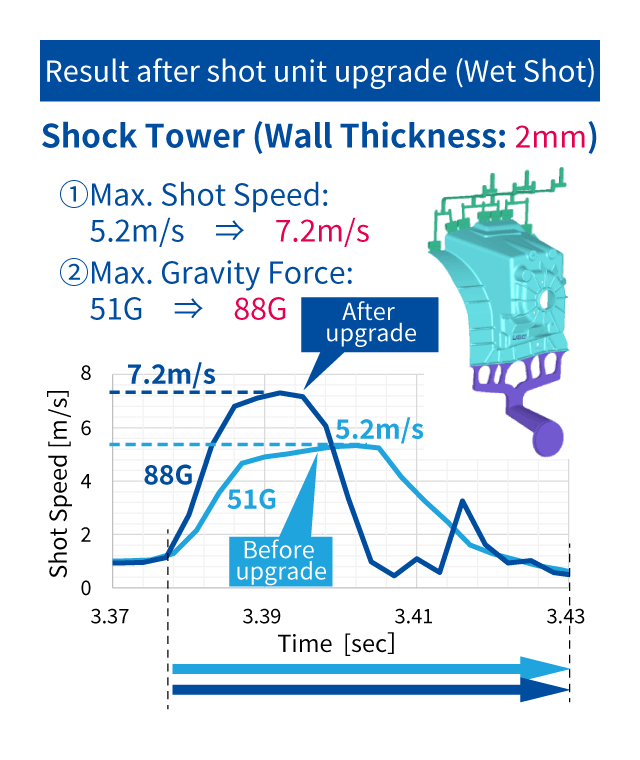
Verified increase in the shot unit capacity under dry and wet shot conditions
Shot Sleeve Vacuum System SleeVac
- Vacuum system to vacuum air inside the shot sleeve and die from sleeve ports
- Exhaust large volume gas in a short time
- Multiple large-diameter suction ports on the sleeve enable large volume exhaust in a short time
Vacuum attainment rate of 95 kPa or less within 1 second when used in combination with a chill vent vacuum - Direct exhaust of lubricant combustion gas inside the sleeve to prevent solidification ahead of shot, which is a problem in vacuum die casting
- The unique design tip UBE developed by UBE significantly reduces vacuum clogging.
- Suitable for making large structural products with thin wall
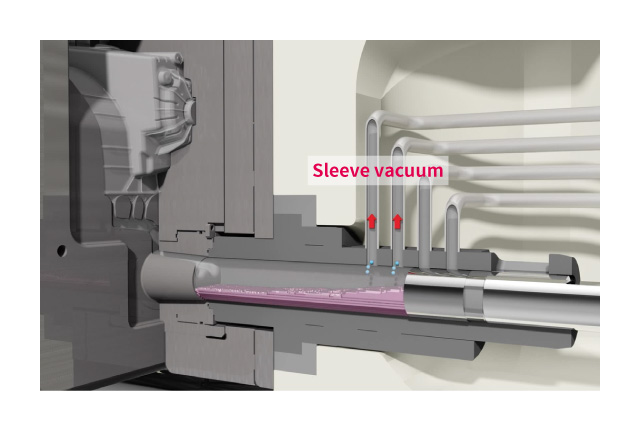
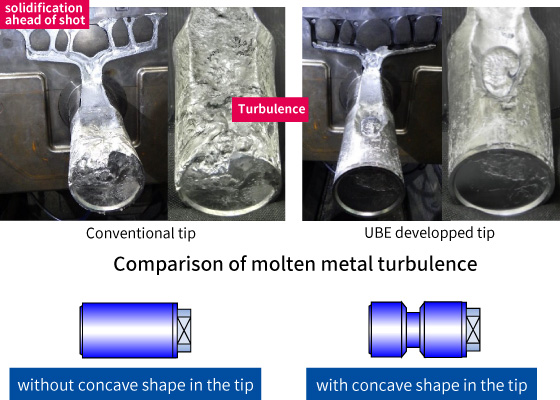
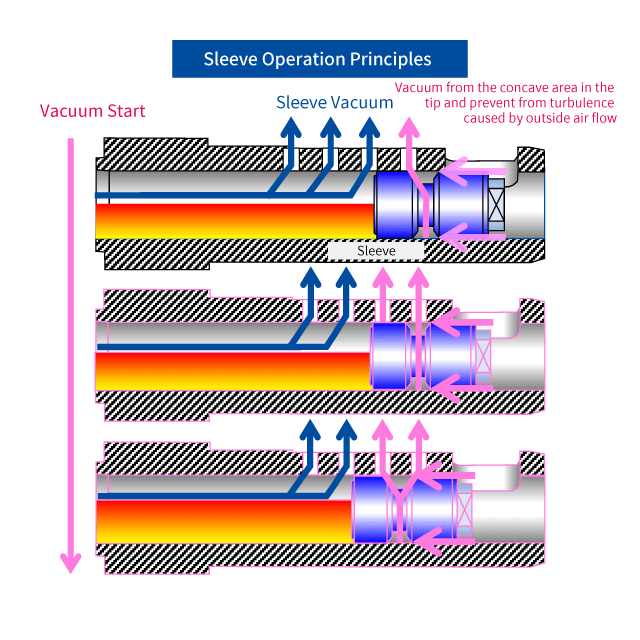
Carbon neutrality by the production process
High cycle machine technology
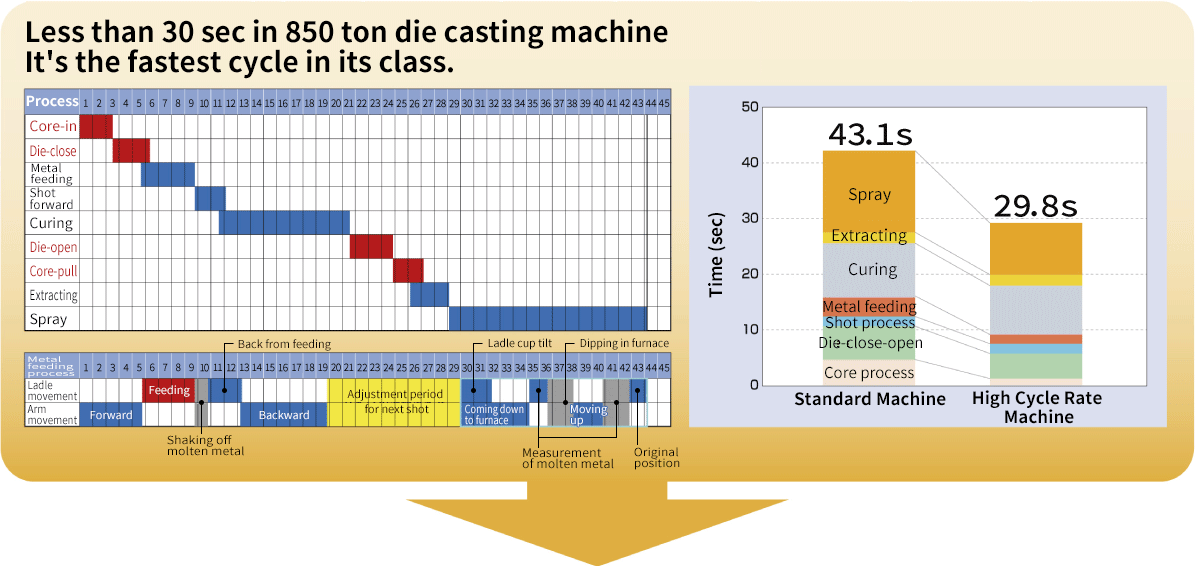
UBE high cycle machine brings contribution to carbon neutrality in components production for electric vehicles that requires life cycle assessment and efficient productivity
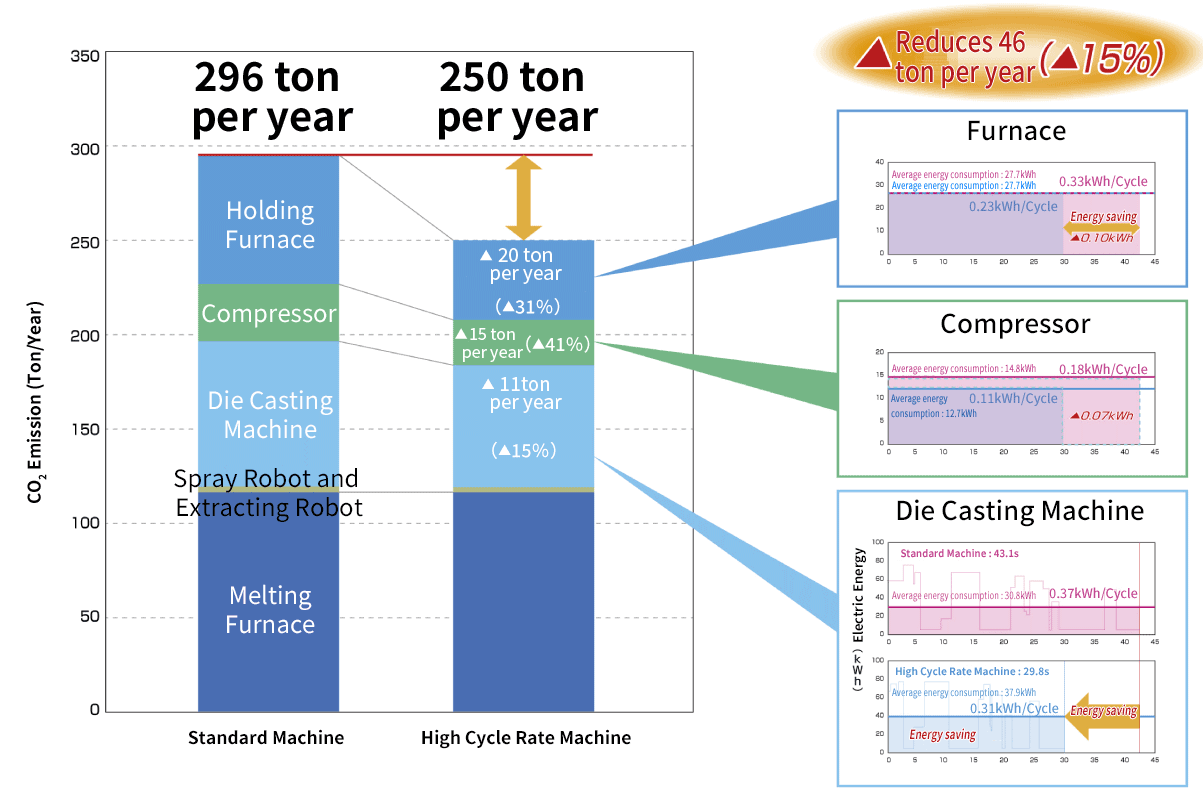
Increased Hydraulic Pump Capacity
Quick cylinder motion by increasing the amount of hydraulic oil discharged from the hydraulic pump
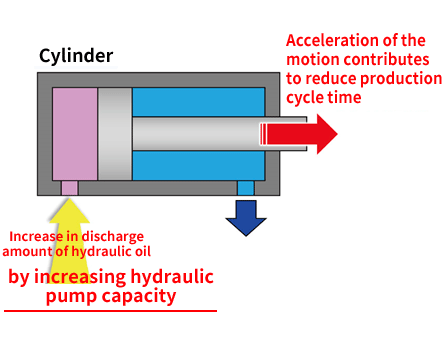
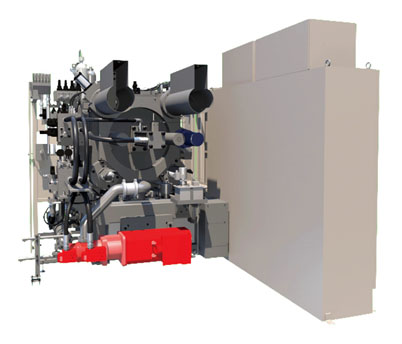
Increased the hydraulic pump capacity and discharge oil volume by servo motor rotation speed control
Achieved cycle time reduction in die closing-opening motion and core motion
Enlarged Hydraulic Pipeline Diameter
Reduced resistance provides smooth hydraulic flow
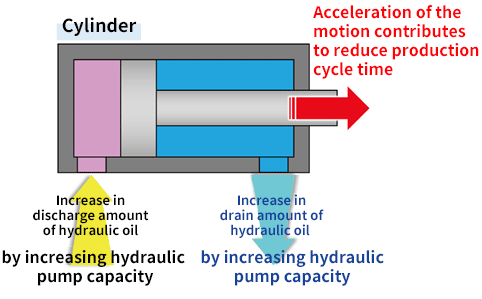
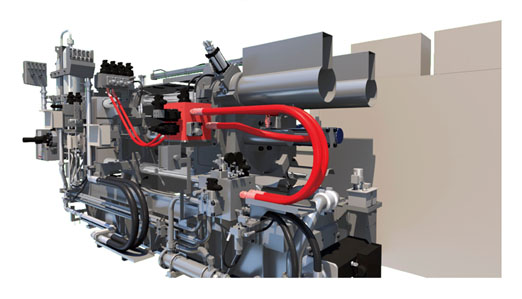
Enlarged pipeline diameter to reduce pipeline resistance due to increased discharge volume
Smooth drainage of hydraulic oil without resistance to improve efficiency of cylinder operation
Maximizes the effect of increased pump capacity and contributes to energy savings by further reducing pipeline resistance
Hydraulic Core Run-Around Circuit
Distributes more hydraulic oil than the pump can deliver to the cylinder
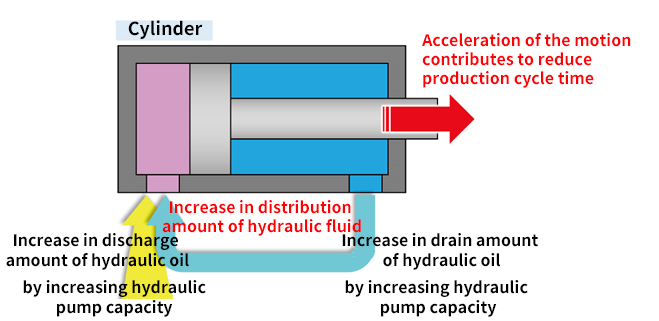
Ube's specialty run-around circuit is used to supply more hydraulic oil to the cylinder than the pump discharge volume
Achieves both energy savings and shorter production cycle times
Mold Opening Intermediate Stop
Normal Operation

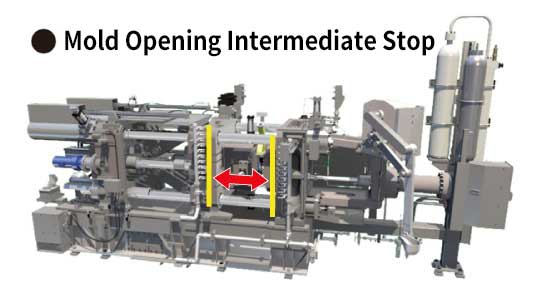
Ube's precise control technology enables intermediate stop of die opening motion even with hydraulic toggle mechanism
In addition to shortening the mold opening and closing time, the fixed and movable dies can be sprayed at the same time, which further reduces the production cycle time significantly
Auto Ladler Driven by Servo Motor
Achieved superfast ladling operation without molten metal spill
Precise control of ladle angle and arm speed when delivering molten metal to the sleeve
Achieved the fastest molten metal conveyance without spills
Servo motor used in conventional auto ladler, which is an alternative to multi-axis ladling robots