History of UBE Die Casting Machine
- Manufacturing excellence with a reliable team of engineers and plant personnel -
Since its inception in 1960, UBE Machinery's die casting machine business has continued to study and accumulate technologies, and has delivered die casting machines to the world while partnering with our customers. As a leading die casting machine manufacturer, we continue to provide high-performance, high-quality die casting machines that are applicable globally, while meeting the trust and expectations of our customers.
History of UBE's Die Casting Machine Business
Beginning of Die Casting Machine Business
The die-casting machine business began as the company sought to enter a new field of machine manufacturing away from the production of coal-drilling-related machinery, which was the company's core business at the time. The die-casting machine business began in 1960 with a technical alliance with Lake Erie Corporation, a U.S. hydraulic press manufacturer. Manufacturing began on die-casting machines based on the belief that "aluminum products for the automobile industry will develop rapidly in Japan."
In 1962, UBE received an order for its first machine, an 850-ton machine. The following year, UBE received an order for a 2,200-ton die casting machine with the world's largest clamping force at that time, based on Lake Erie technology with UBE's own innovations and improvements. In the same year, at a time when in-house die casting was not yet the norm for automotive companies, UBE made a sales pitch, including technical explanations and post-installation technical support, and received an order for its first 1,200-ton die casting machine for an automotive company. This was the beginning of UBE's die casting machine business, and the company expanded its sales to domestic automotive and die casting manufacturers.
1962
The first die casting machine (die clamping force: 800 ton) was completed.
Developed the largest (at the time) die casting machine in Japan
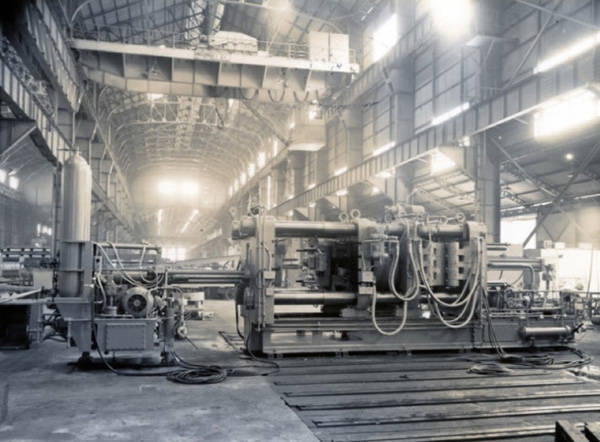
1963
Manufactured the world's largest (at the time) die casting machine
Delivered a die casting machine with a clamping force of 2,200 tons as a general-purpose machine
Progress in Unique Technology
The late 1970s and early 1980s were devoted to the development and establishment of new technologies.
After the first oil crisis, we believed that "in the future, the automotive industry will move toward reducing fuel consumption, and the use of aluminum parts will increase as a means of reducing weight," and we developed various technologies to achieve these goals more efficiently with higher quality.
In 1976, the company developed the "UNI-FF", which aimed to simplify the finishing process by reducing the number of casting burrs and to save labor through unmanned operation.
In 1982, the company developed the "GF System" to reduce voids in transmissions for AT vehicles, whose production was increasing at the time.
In 1976, the company developed a squeeze casting machine to produce lightweight aluminum wheels for automobiles.
The idea was to combine the advantages of casting and forging, UBE realized a fully automated system capable of producing products with quality comparable to that of the forging process.
This unique development, which combined the accumulated equipment technology with the viewpoint of casting technology, had a great impact on users in Japan and abroad, and UBE's die casting machines continued to advance.
1976
Developed "UNI-FF" anti-burrs breaking shot mechanism
The first computer-controlled, fully automatic die casting machine in the world.
Computerized aluminum casting, mold spraying, and take-out processes
Received orders from domestic automotive industry, etc.
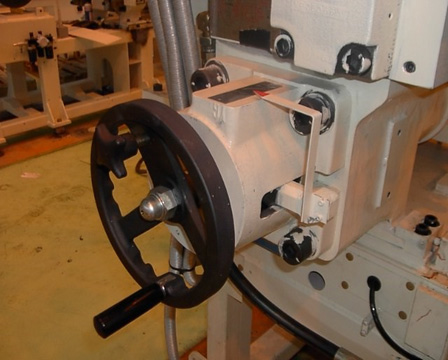
Developed the first squeeze casting machine.
Aimed to produce aluminum wheels for automobiles.
Increased sales by gaining industry recognition for greater design freedom compared to the old method.
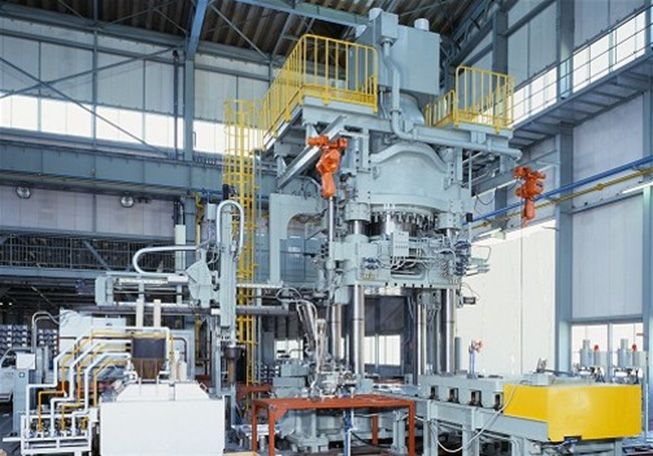
1978
Establishes UBE Industries (America) Inc.
First U.S. office established in New York City for sales and service of UBE products
1982
Development of a new vacuum die casting method "GF (Gas Free) System”
Structure that eliminates air entrapment, which causes blowhole as much as possible.
Features such as casting at one-half to one-third the metal pressure of conventional molds.
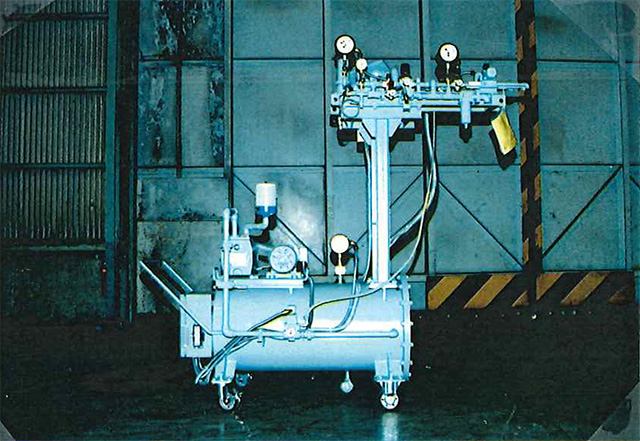
Expanding into the U.S. market and gaining a foothold overseas
By the 1970s, UBE had won numerous orders, including from automobile manufacturers, and had improved its position in the Japanese market.
However, when it turned its attention overseas, it found that there was little confidence in products that had not been sold in Europe and the U.S., and it was not even allowed to enter the U.S. market.
Therefore, the company turned its attention to cultivating the U.S. market.
In 1979, we received a large order from Ford, one of the "Big Three" automakers. The company was then able to expand its supplier base to GM. This was the result of UBE's technical capabilities, which were highly regarded for improving the quality of the "UNI-FF" burr-free die-casting machine.
1984
Established UBE Industries America Michigan branch office (Ann Arbor Michigan)
Establishment of a service base for the molding machine business in Ann Arbor, near Detroit, USA, laying the foundation for today's North American business.
In 1992, the Michigan branch became independent as UBE MACHINERY SALES INC. and expanded its office and warehouse.
1996 Company name changed to the current "UBE MACHINERY INC.
Established a manufacturing plant to provide engineering, manufacturing and support services, and began assembling die casting machines and injection molding machines.
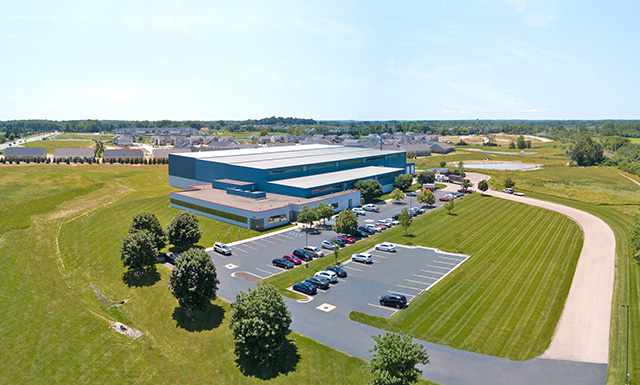
Secure our foothold and venturing into new areas
The Plaza Accord (1985 agreement among the G5 nations) led to the appreciation of the Japanese yen, and in the second half of the 1980s, Japanese industry shifted from an export-oriented focus to domestic demand.
Under these circumstances, UBE supplied many machines to overseas automakers in recognition of its solid technical capabilities, developed new small and medium-sized machines for the domestic market, and improved and expanded its product lineup to meet the demand for lighter and more powerful automotive parts and higher-quality electronic equipment parts.
We also developed the world's first squeeze casting machine equipped with a horizontal mold clamping x vertical injection mechanism, and expanded our business scope to include pressure-resistant and heat-treated parts.
This period laid the foundation for UBE's technology, which continues to this day by listening carefully to customers' needs and challenging them with unprecedented ideas.
1986
Toggle Type Die Casting Machine "G Series"
(Die clamping force: 140 to 800 tons)
Completely redesigned machine with improved space productivity and shorter dry cycle time due to reduced overall length
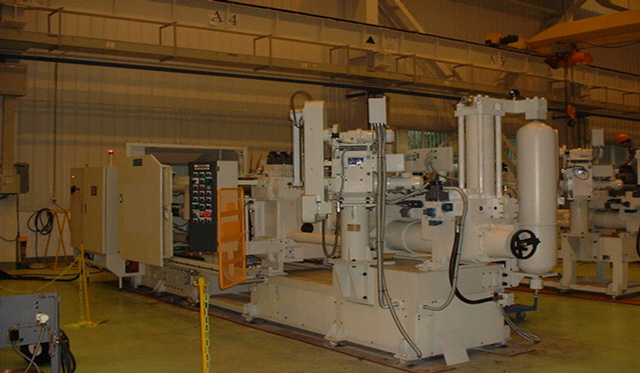
1986
Squeeze Casting Machine "HVSC Series"
(Clamping force: 250 to 850 tons)
World's first squeeze casting machine with horizontal die clamping and vertical injection mechanism
Features a combination of conventional die casting and molten metal forging methods, making it suitable for pressure-resistant and heat-treated parts
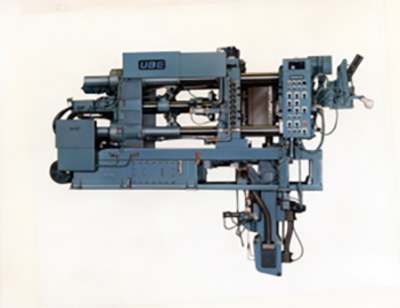
1987
Delivered the world's largest (at the time) die casting machine with a clamping force of 4000 tons to a domestic user.
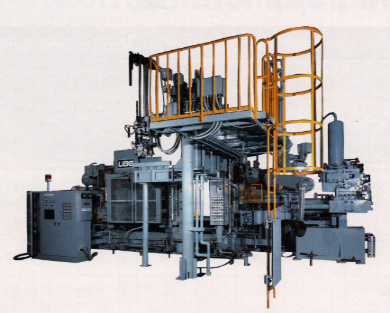
Become a global standard machines to fly out to the world.
The Japanese economy had been in recession since the 1990s. Private capital investment lost momentum, and the appreciation of the Japanese yen dealt a severe blow to export industries. In order to overcome this period, save our strength, and make a great leap forward, we decided to develop a new model of machines with completely new software and hardware.
With the goal of stabilizing the work environment and improving product quality, we were able to develop a prototype machine that incorporated next-generation technologies such as injection control technology using our proprietary servo valves and quick toggle mechanism.
In the 2000s, the company completed a global standard machine that has been improved and developed and has been well received both in Japan and overseas.
The global environment is still changing. Our challenge continues to this day.
1997
Toggle Type Medium Die Casting Machine "NX Series"
(Die clamping force: 350 to 850 tons)
Revolutionary machine equipped with many next-generation technologies, such as "S-DDV" using servo motors for injection speed control, quick toggle, and wide platen
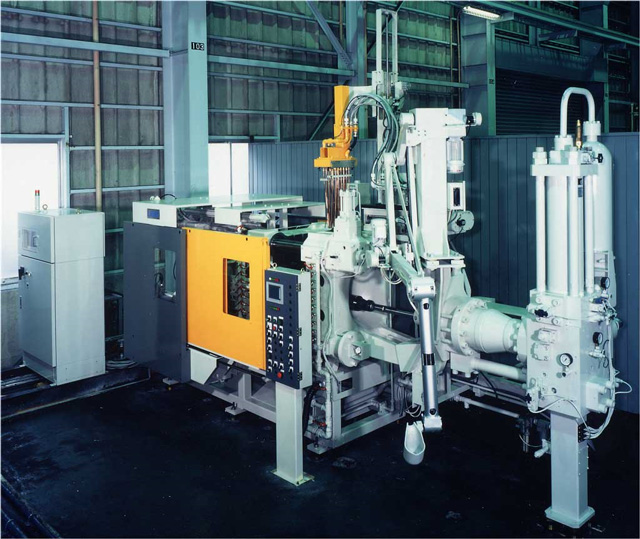
2001
Established UBE Machinery (Shanghai) Co.,Ltd
Established as a base for integrated production, sales and service in the expanding Chinese automotive market
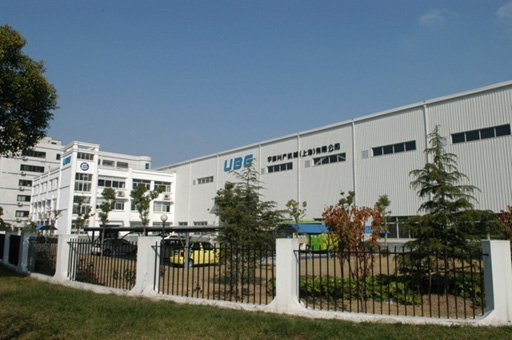
2002
Toggle Type Medium Die Casting Machine "iS Series"
(Die clamping force: 375 to 850 tons)
Mid-range global standard machine with further enhanced next-generation technology from the NX series.
Featuring the industry's largest die clamping force, greatly improved basic injection performance and touch panel operation
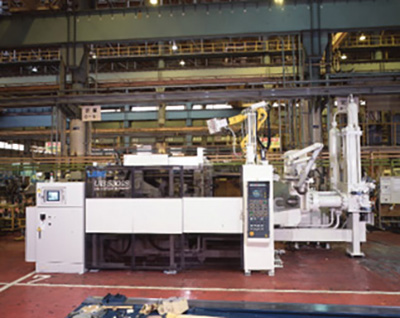
2006
Developed "UH Series" large-size hybrid die casting machine
(Clamping force: 1250 to 2500 tons)
Space-saving through the use of 2 platens and the industry's first tiebar removal device on the injection side.
Energy-saving machine with hybridized hydraulic and electric clamp movement and servo pump as standard equipment
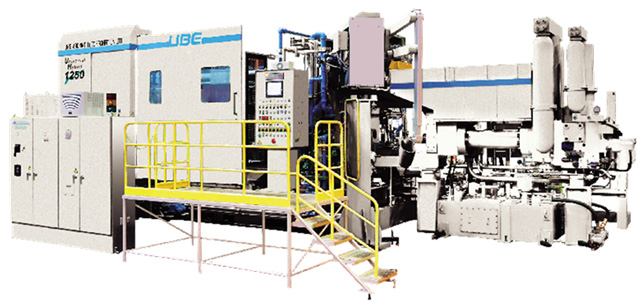
2010
Development of Large Hydraulic Toggle Type Die Casting Machine "iV Series"
(Die clamping force: 1250 to 3550 tons)
Large global standard machine equipped with energy-saving servo pump I-StopServo as standard.
Newly developed HS-DDV injection control valve achieves ultra-high-speed injection of 10 m/s and can be used for all kinds of products.
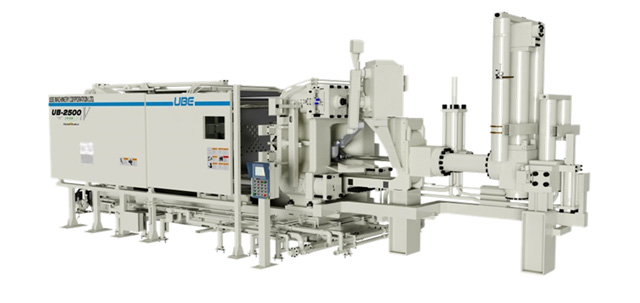
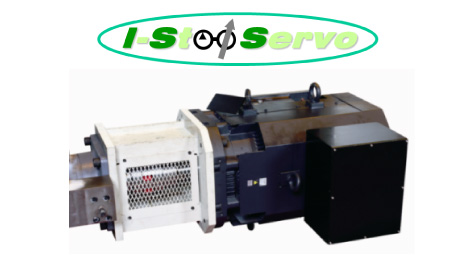
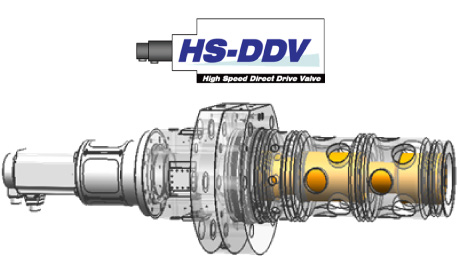
2010
Development of the "iS2 Series" the successor to the popular iS machines
(Clamping force: 375 to 1100 tons)
User-friendly switch-type operation panel with improved operability and visibility
First 1100-ton die clamping force machine lined-up in its industry (at the time)
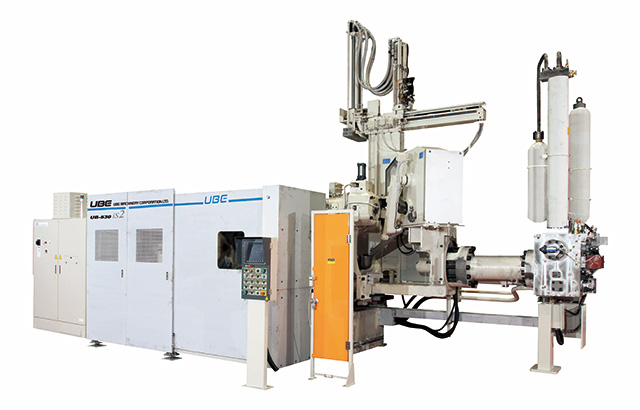
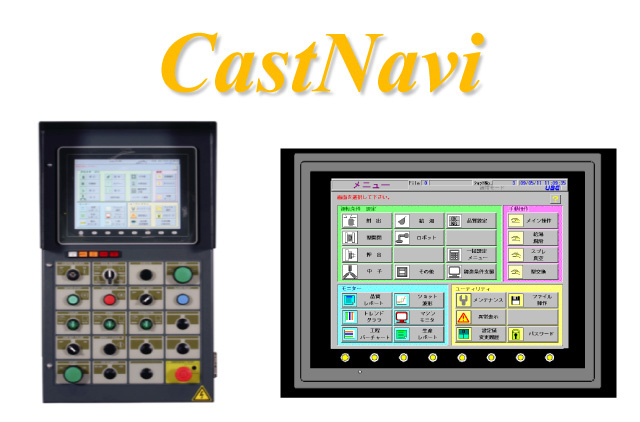
2014
Developed "HFC" a hybrid machine for die casting and low-pressure casting
New concept machine that utilizes both pneumatic and hydraulic pressure in the filling process of "low-pressure casting" × "squeeze".
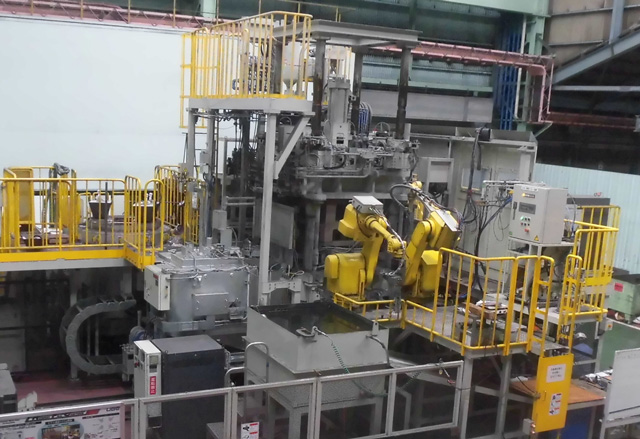
2016
Development of environmentally harmonious Die Casting Machine "iS3 Series"
(Die clamping force: 530 to 1300 tons)
Optional electric clamping and energy-saving servo pump as standard equipment contribute to CO2 reduction.
Newly developed S-DDVII injection with increased performance can be used for various EV components.
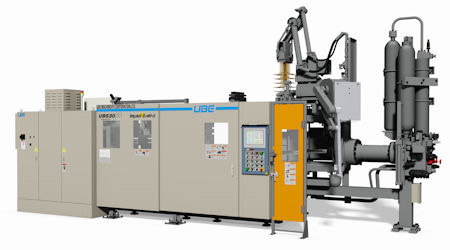
2022
Large-sized hydraulic toggle die casting machine "iV2 Series" developed
(Die clamping force: 1250 to 6500 tons)
New large-size global standard machine specializing in improving productivity and product quality by improving the ICT technology of the long-selling iV series.
Newly developed ES injection system achieves shorter filling time compared to conventional die casting machines.
The first die casting machine in Japan with a capacity of 6500 tons was launched.
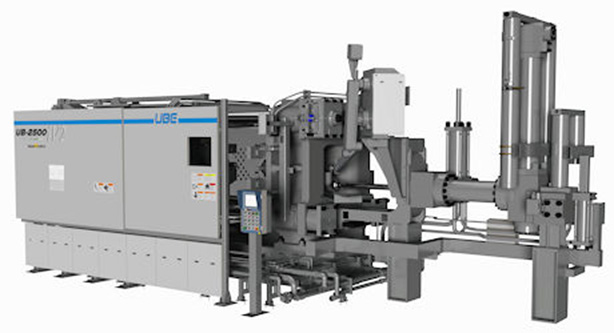