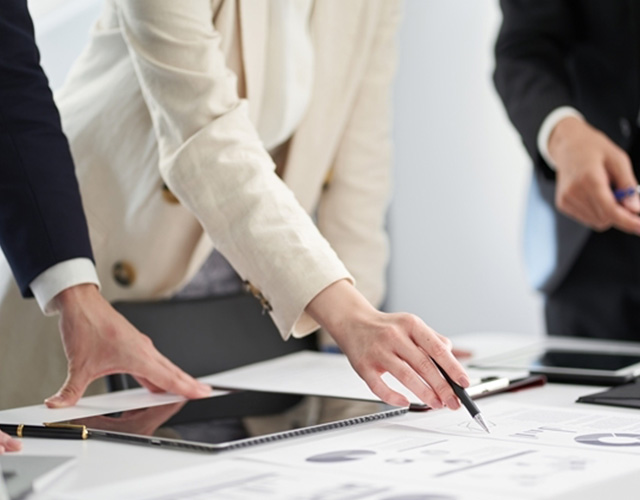
UBE Die Casting Machines
Quality Improvement and Technology
We will continue to respond to our customers' requests by examining them from various angles in order to help solve their problems and improve the quality of our products.
Sleeve vacuum: SleeVac
- Vacuum system to vacuum air inside the shot sleeve and die from sleeve ports
- Exhaust large volume gas in a short time
- Multiple large-diameter suction ports on the sleeve enable large volume exhaust in a short time
Vacuum attainment rate of 95 kPa or less within 1 second when used in combination with a chill vent vacuum - Direct exhaust of lubricant combustion gas inside the sleeve to prevent solidification ahead of shot, which is a problem in vacuum die casting
- The unique design tip developed by UBE significantly reduces vacuum clogging.
- Suitable for making large structural products with a thin wall
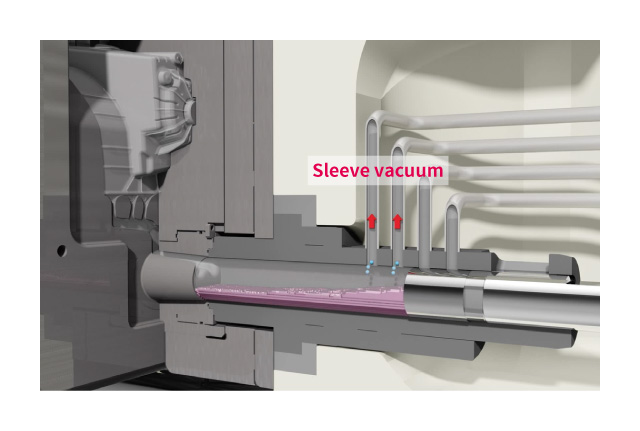
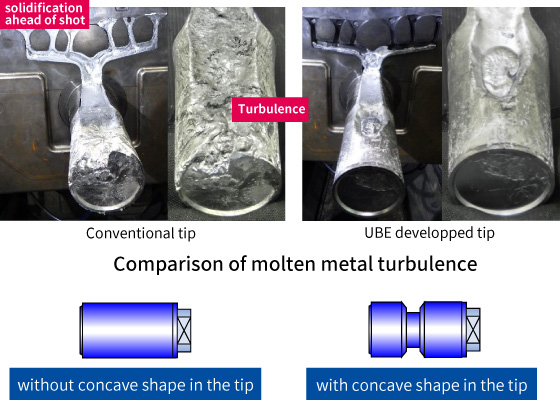
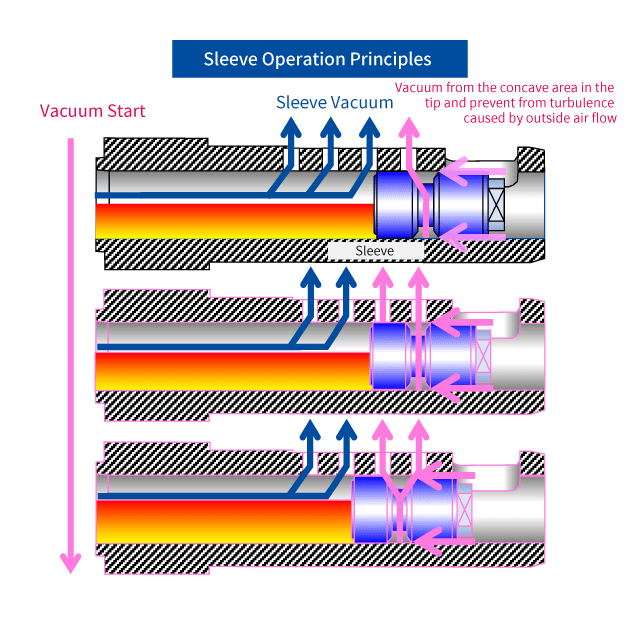
GF Vacuum Casting System
Effects of the GF Process
Effects of GF Vacuum Die Casting Method
1) Prevention of entrapment: Prevention of gas leakage
⇒Elimination of impregnation process ⇒Cost reduction2) Improvement of hot water circulation by suppressing gas accumulation in the final filling section
⇒Good product rate increase3) Elimination of gas on the inner surface of the mold
⇒reduction of metal pressure and high speed to obtain good products
⇒prevention of burr formation ⇒higher operation rate.
Overview of GF Vacuum Casting System
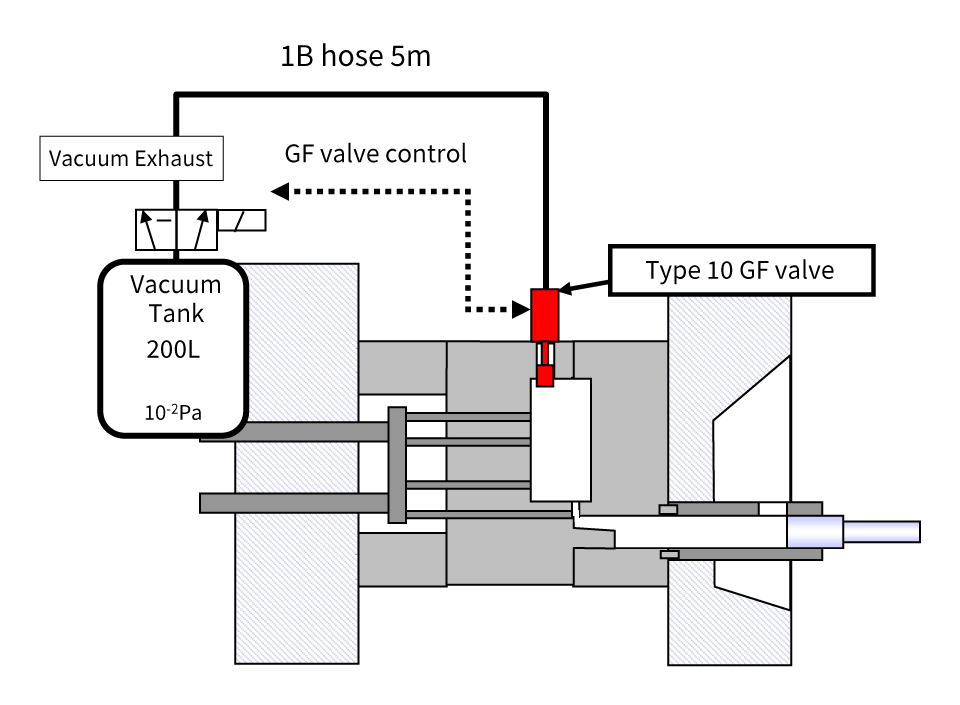
- 0.3-0.5sec before high speed start of vacuum
- Attained vacuum 20kPa
- Gate shot is the basic method
- On large machines, cavity shot is often done at low speed up to 20-30% of the product area.
0.3s-20kPa
Atmospheric pressure: 100kPa
1/5 of atmospheric pressure
Vacuum Sealing Methods | Vacuum Valves | Metal pouring method | |||
---|---|---|---|---|---|
Parting surface | Ejector pin section | Core part | Injection part | ||
No seal | No seal | No seal | No seal | GF-10 tyep valve | Ladle pouring |
Operation flow of GF Vacuum Casting System
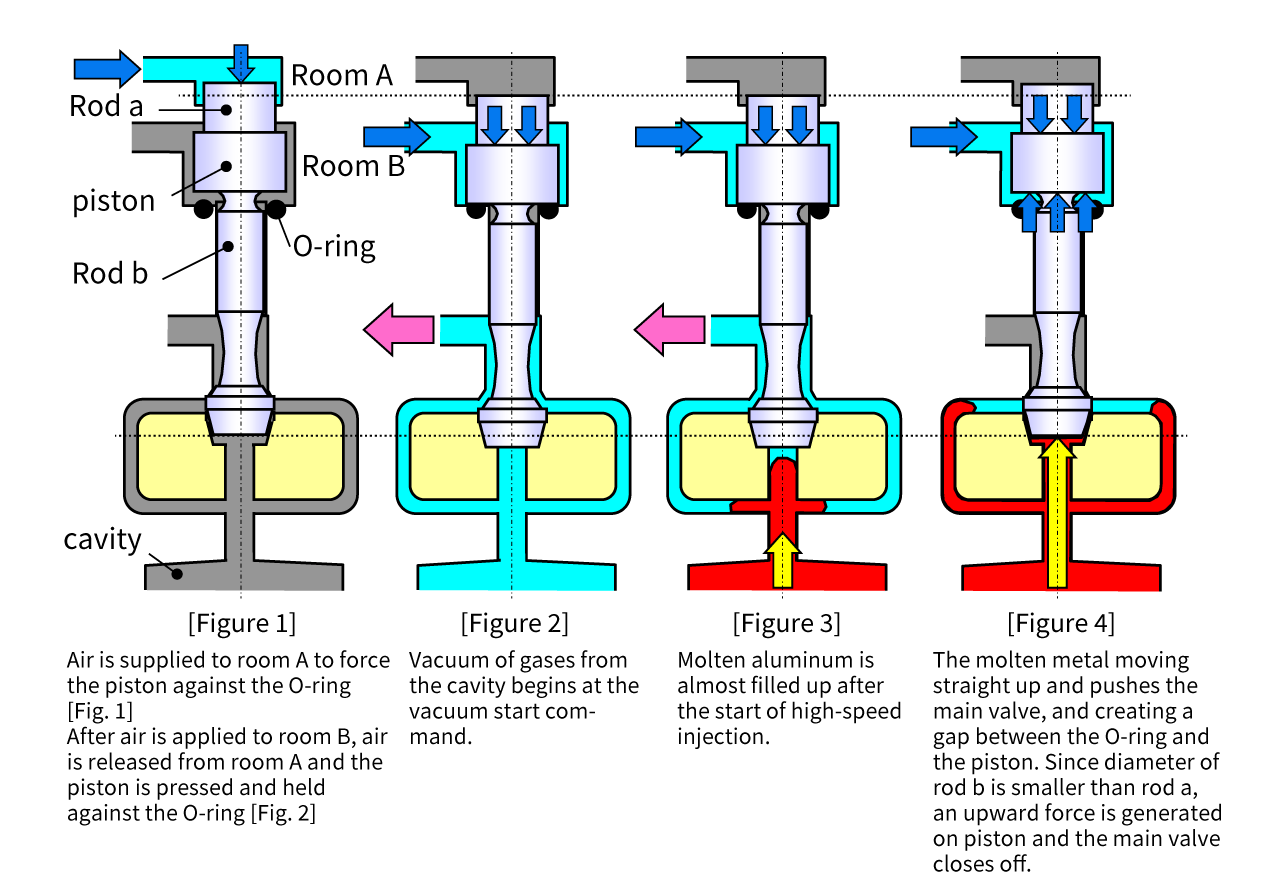
Introduction of "ADSTEFAN"
We propose the most suitable die casting machine, die casting process, mold plan, casting conditions, etc., according to customers' requirements and product quality requirements. For die casting, the casting simulation system "ADSTEFAN" is used to study the die casting process. ADSTEFAN is a registered trademark of Hitachi Industrial Control Solutions Co.
Die casting simulation software: ADSTEFAN
ADSTEFAN is a support tool that provides timely direction for mold plan design. ADSTEFAN meets the requirements of the die casting shop, contributing to quality improvement, productivity improvement, lead time reduction, and skill transfer in a wide range of areas.
We support the die casting site by linking our accumulated casting technologies with ADSTEFAN to predict various casting phenomena.
Features of ADSTEFAN
Outstanding Analysis Speed
The industry's fastest solver can quickly reproduce casting phenomena and reflect them in the mold design in a timely manner. Parallel processing capability further improves analysis speed.
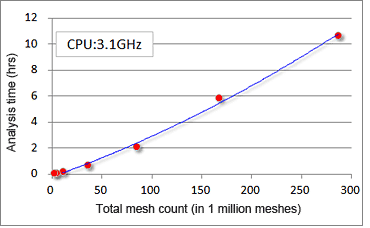
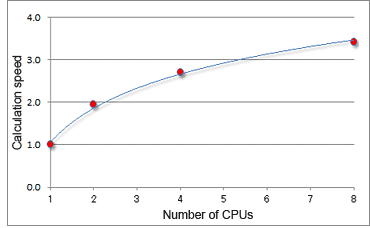
Accurate & highly reproducible analysis
Solver development in collaboration with an external organization with a proven track record.
Achieve high analysis accuracy through consistency verification.
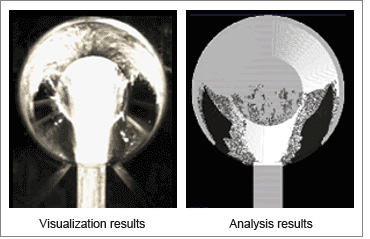
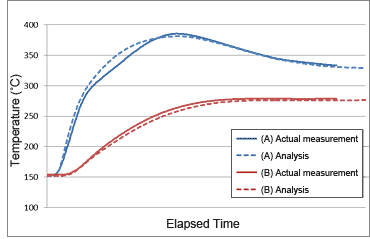
Full range of analysis capabilities
Reproduce various phenomena at the die casting site with the full range of analysis functions.
Metal flow analysis
- Metal flow analysis
- Back pressure, gas-liquid 2-phase flow (considering metal pressure)
- High-precision metal flow analysis (mixing elements, CIP)
- Sleeve analysis of molten metal behavior
- Surface tension consideration
Solidification analysis
- Solidification analysis (molten metal addition function)
- Shrinkage shape analysis
- Local squeeze analysis
Others
- Mold temperature analysis (internal cooling, spray consideration)
- Thermal stress analysis
- Heat treatment analysis
- Inclined casting
- Continuous casting
- ESR analysis
- Temperature mapping function
Simple operation system
Easy operation allows smooth handling from geometry creation to result evaluation.
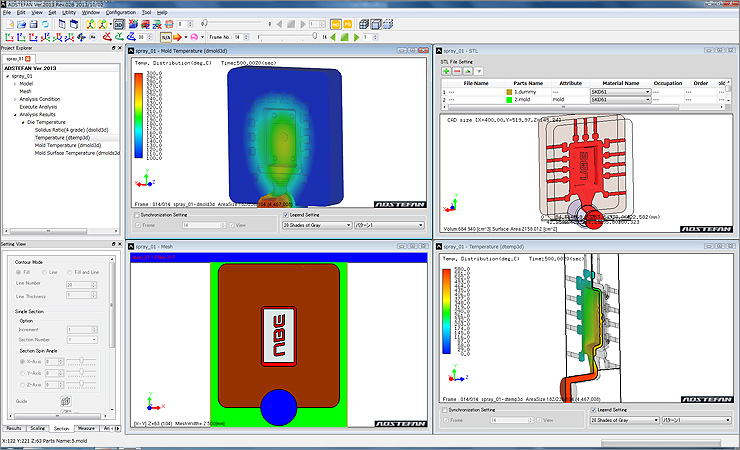
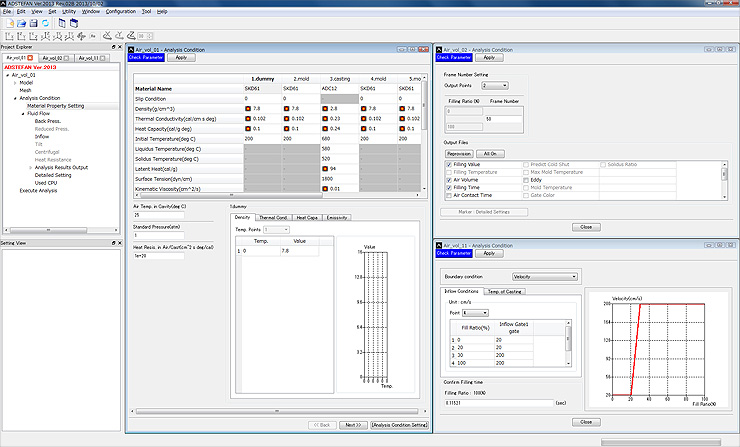
Casting Machine Manufacturer Support
UBE Machinery engineers provide support from the perspective of casting technology.
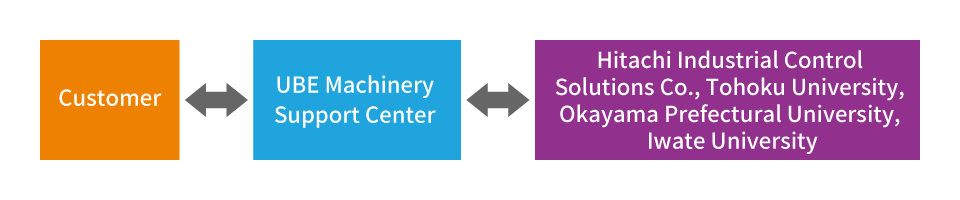
Compatible with a wide range of processes
We support a wide range of casting processes, including gravity casting, low-pressure casting, and die casting.
- Die casting (squeeze, semi-solid)
- Gravity casting (sand, mold)
- Centrifugal casting
- Vanishing model casting
- ESR (Electroslag Remelting)
- Low pressure casting
- Gradient casting
- Continuous casting
- Precision casting
Application example of "ADSTEFAN"
Cooling method design preventing mold and product problems before they occur
Internal Cooling Design
UBE's unique parameters allow highly accurate prediction of steady state mold temperature distribution, taking into account cooling holes. This allows us to verify the temperature balance of the mold, prevent seizure points, and reduce cycle time.
It examines the diameter and depth of the cooling holes, as well as the temperature and flow rate of the cooling water. The size and location of shrinkage are predicted in advance to achieve the optimal internal cooling design.
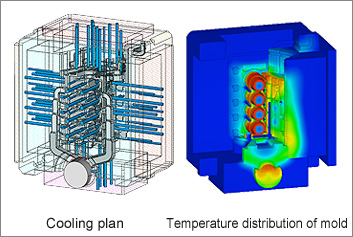
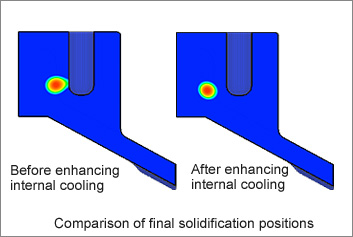
Externally Cooled Design
Predicts mold temperature distribution based on spray pattern, distance, angle, and pressure. Optimizes mold temperature balance under spray conditions to prevent soldering and reduce cycle time.
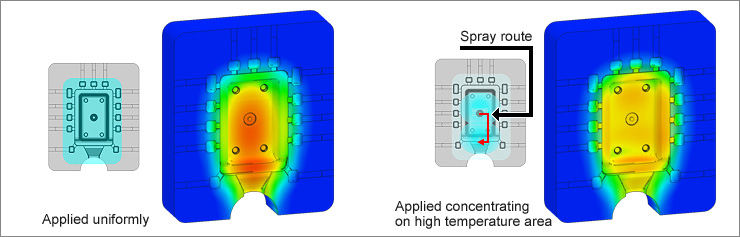
Gate and Runner Design Predicting Behavior and Going Prototype-Free
Gate and runner design
Predicts gate/runner shape problems by analyzing flow and solidification. Optimal design of gate/runner shapes is realized based on various evaluation indices such as filling behavior, gate inflow balance, and solidification shape.
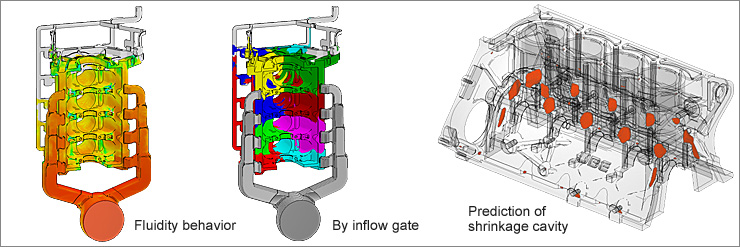
Injection parameter plan
Predicts molten metal behavior in sleeves and molds based on injection conditions that take into account pouring and machine characteristics. It can determine in advance if molten metal will be disturbed or temperatures will drop, and optimize the setting of conditions.
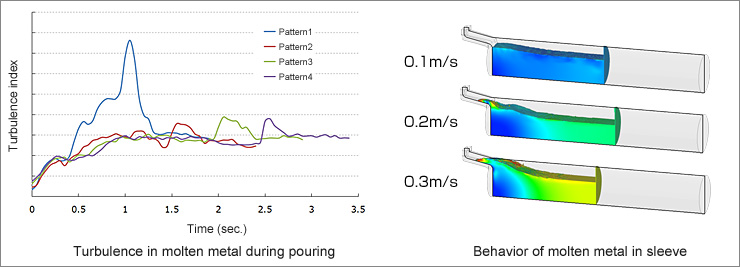
Designing air ventiration Routes Identifying Residual Gases and Determining ventiration Conditions
It designs ventiration routes by predicting the amount of residual gas in the product. It can optimize ventiration conditions by comparing and evaluating different ventiration processes, including our GF vacuum system.
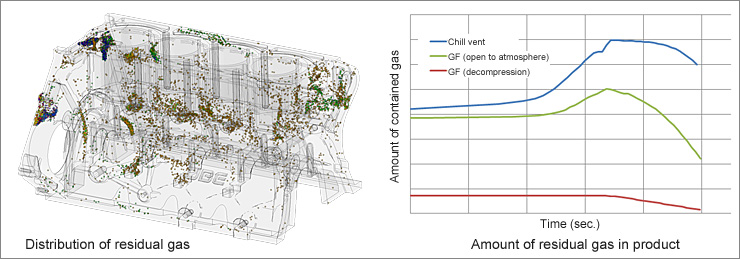
Local Squeeze Design Eliminating Shrinkage in the Analysis Phase
Local squeeze analysis predicts the effect of sqeeze pin. Optimization of squeeze pin size, squeezing timing, and speed is achieved.
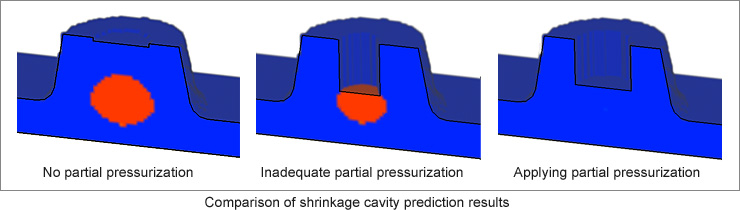
Contract Analysis Service (Chargable)
Our design and analysis professionals, who have experience in designing more than 50 products per year, will propose reliable solutions.
Membership Casting Analysis Service
With an annual contract, up to three designs can be analyzed and reviewed free of charge; the fourth and subsequent designs are charged at half the normal cost.