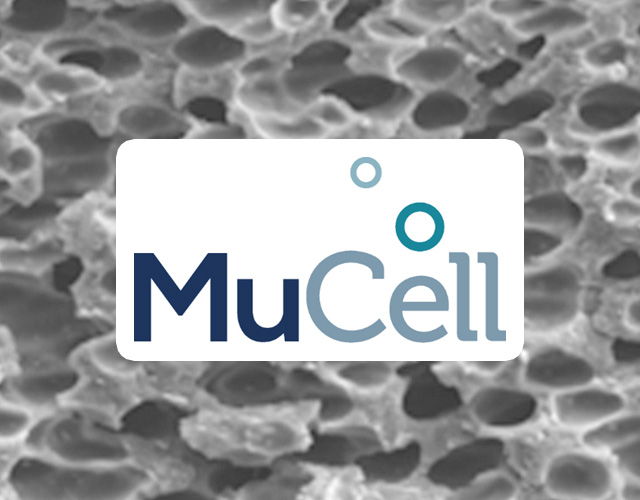
UBE Machinery's Injection Molding
- MuCell® - Microcellular Foam Molding
MuCell® microcellular foam molding, which uses nitrogen gas as the foaming medium, is a foaming molding method that realizes carbon-free foaming, and is a technology that offers further possibilities from conventional foam molding in terms of flow extension and foaming force, which are gas dissolution characteristics, due to the critical pressure effect.
Since the launch of MuCell®, we have started to develop a screw that can both improve gas dispersion performance as well as general-purpose moldability, and we offer molding systems equipped with UBE Machinery's unique MuCell® screw.
*MuCell® is a registered trademark of TREXEL, Inc.
MuCell® microcellular foam molding is a technology first conceived and invented at the Massachusetts Institute of Technology (MIT) in the U.S. It is a molding method that uses supercritical gas (SCF) to generate microcells (microbubbles) inside molded products, contributing significantly to improved molding quality, weight reduction and shorter cycle times.
The MuCell® process can be introduced either by purchasing a new injection molding machine with MuCell® specifications or by modifying it. As a partner of TREXEL, Inc., which holds an exclusive license for this technology, we have a license agreement with TREXEL, Inc. and can offer the option of using UBE injection molding machines equipped with UBE Machinery's proprietary MuCell®-designed screw.
Molding trials are also available at the IM Solution Center at our Nagoya Machinery Works.
Main equipment of MuCell® process
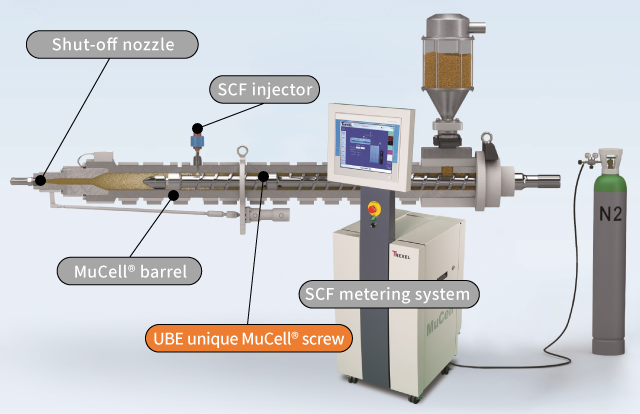
Cross-section of foam molded product
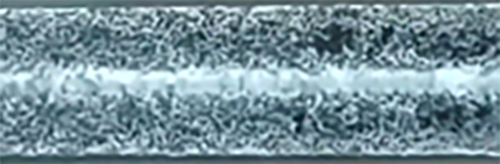
Comparison of expected effects of MuCell® microfoam and chemical foaming
MuCell® | Chemical foaming | ||
---|---|---|---|
Foaming Gas | Type | CO2 or N2 | CO2 |
Injection method | Direct | Foam M/B mixture *M/B: Master batch |
|
Dissolved amount (concentration) | Large | Small | |
Resin viscosity decrease | Large | Small | |
Foaming pressure | Large | Small | |
Flow length elongation | Large | Small | |
Reduction of injection pressure and clamping force | Large | Small | |
Reduced sink marks and warpage due to foam pressure | Large | Small |
Example of Molded Products
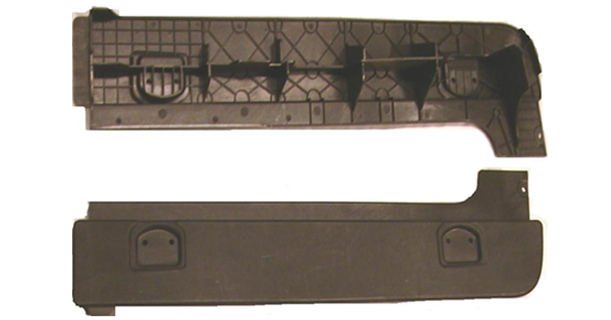
Product: | Trunk Liner (Automotive) |
---|---|
Material: | PP+GF |
Weight reduction rate: | 10% |
Clamping force reduction rate: | 40% (1000t⇒600t) |
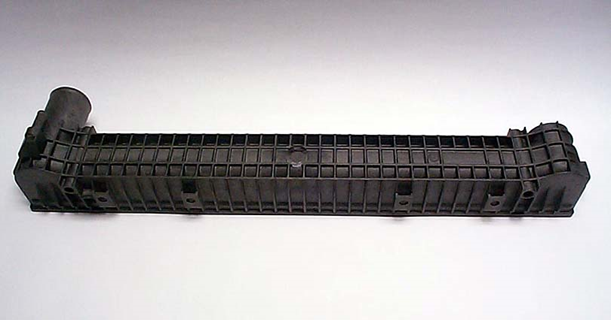
Product: | Radiator end tank (Automotive) |
---|---|
Material: | PA+GF |
Weight reduction rate: | 15% |
Molding time reduction rate: | 25% |
A purchase agreement for SCF feeder (including patent license) is required to use MuCell® technology. For additional details, please contact Trexel,Inc.