UBE Machinery's "Screws"
“UBE Machinery's Screws" that meet diverse needs with our experience and technology.
We offer a wide variety of screw variations developed by combining the experience and technology accumulated by UBE Machinery over many years. We have also inherited the technology cultivated in our 60-year history of screw manufacturing at our Nagoya Plant, which enables integrated in-house production using machining, surface treatment, thermal spraying, and screw-specific equipment to manufacture the largest and highest-quality screws.
UBE Machinery's Various Screw
UBE Machinery has the facilities for integrated in-house production of screws, the most important component of injection molding machines, which greatly affects the quality of molded products. We offer a wide variety of high-quality screws.
Variety of screws designed for different applications
UB screw(for multi-purpose)
“UB Screw” (Ultra Barrier Screw), the optimal design for customer's multi-purpose applications. Unique double flight design realizes overwhelming plasticizing capacity.

Contributions to our Customers
- Supports a wide range of molding from general-purpose plastics to engineering plastics.
- High plasticizing capacity" contributes to high-cycle molding.
- Homogeneous melting" achieves high molding quality.
Application Examples
-
Automobile parts
Bumper, Instrument panel, Headlamp lense, etc.
-
Home appliances/OA parts
PC, LCD TV, etc.
-
Industrial Material parts
Pallet, Container, etc.
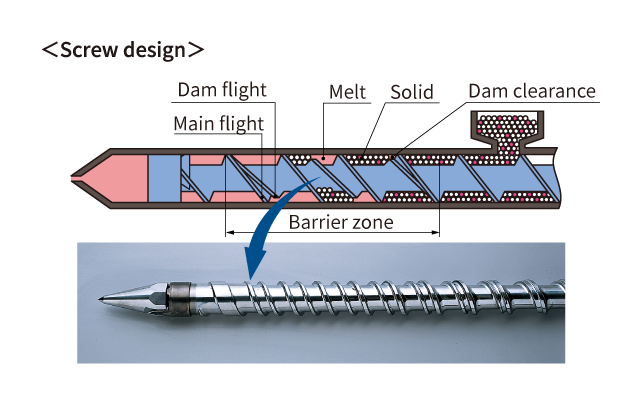
- Our unique screw design, including long barrier and unmelt-less dam shape, high mixing and plasticizing capacity, and energy saving, produce excellent plasticizing performance.
- Unmelt-less plasticization contributes to lower raw material costs, such as high-magnification master batch molding and greater freedom in colorant selection.
SP III Screw(for PP high-cycle molding)

Contribution to Customers
- “PP-oriented high plasticization capability” contributes to high-cycle molding.
- “High master batch compatibility” with high dispersion mixing elements contributes to lower material costs.
Application Examples
-
Automobile parts
Bumper, Instrument panel, etc.
-
Industrial Material parts
Container, etc.
MF-UB screw(for super-high color mixing)

Contribution to Customers
- “Adaptation to high-magnification master batches (200x or more)” contributes to material cost reductions.
- “Quick color change” contributes to rationalization of production.
- “No need for mixing nozzles” realizes lower equipment costs and effective use of injection pressure.
Application Examples
-
Automobile parts
Bumper, Instrument panel, Trim parts, etc.
MD-UB screw(for super-high mixing)

Contribution to Customers
- “Homogeneous mixing” realizes high-cycle molding of PP
Application Examples
-
Automobile parts
Bumper, Instrument panel, Trim parts, etc.
LFT screw(for Long Fiber Thermoplastics)

Contribution to Customers
- Molding of high-rigidity and high-strength parts realized by “function to suppress cutting of reinforcing fibers”.
- Contribution to “weight reduction of automobiles”.
Application Examples
-
Automobile parts
Module parts, etc. (front end, door)
F screw(for low shear, low heat generating)

Contribution to Customers
- Contributing to the molding of transparent parts and optical parts with “high transparency and contamination-free melt quality”.
Application Examples
-
Transparent parts
Light guide plate, glazing, lens, etc.
Screw Production Equipment at Nagoya Machinery Works
- 60 years of quality in large screw manufacturing
(size: φ350mm, L10,500mm). - In-house integrated production using equipment dedicated to screw production.
- Technical variations to meet diverse needs.
- Mirror-finishing technology for screws that improves injection performance.
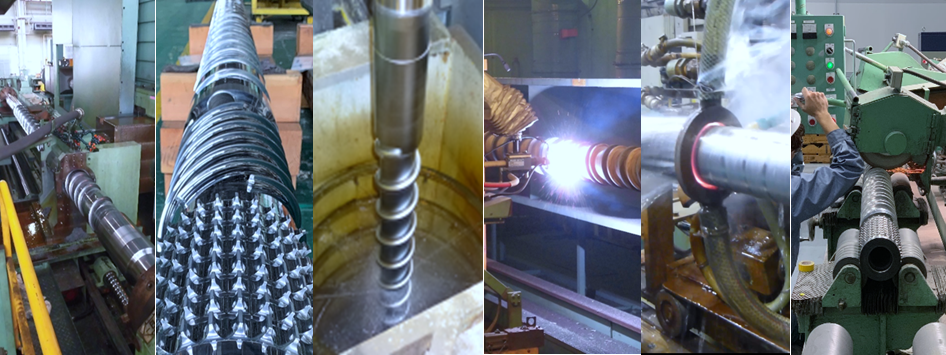