Chemical Equipment
We provide total services including preventive diagnosis, maintenance service, repair, modification, and maintenance history management so that our customers can use our products for a long time.
We provide services not only for our products, but also for other companies' products and equipment, so please contact us for more information.
(In July 2020, we took over the chemical equipment business from Hitachi Plant Mechanics, Ltd.)
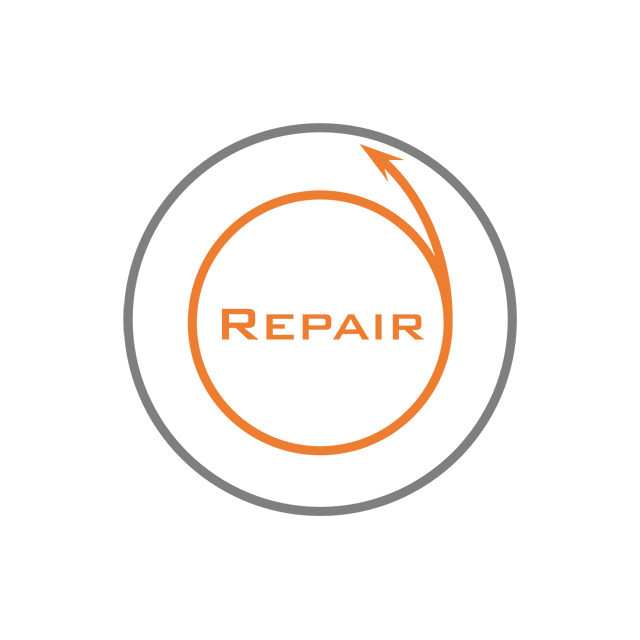
Repair Service
- Restoring your equipment to its original performance -
Supply and Repair of Consumable and Renewable Parts
In addition to the parts we manufacture, we can also quickly supply parts through our various procurement channels, in addition to general parts.
We also hold some special bearings in stock that normally take more than a year to deliver, in case of emergency.
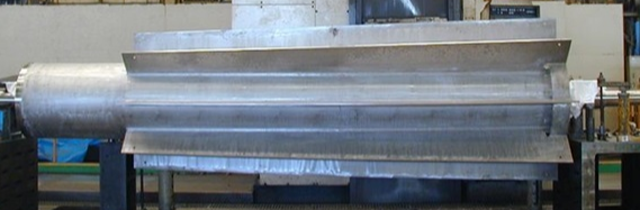
<Examples of procured parts>
- Special bearings
- Mechanical seals
- O-rings
- Gaskets
- Rotors
- Agitator shafts
- Other machined parts used in our equipment
Overhaul
Overhaul is performed onsite for equipment delivered by our company.
Depending on the structure, we may be able to overhaul other than our delivered equipment as well.
We can also propose investigations into the cause of problems, emergency measures, and permanent countermeasures for defects found during overhauls, based on our extensive experience in maintenance.
<Main maintenance examples>
- Overhaul of reactor with agitator
- Overhaul of polymerizer for high viscosity
- Overhaul of centrifugal thin-film evaporator
- Overhaul of centrifugal extractor
On-site repair of rotating shaft
Leaving a damaged shaft unattended can lead to a serious accident.
After many years of use, the mating part with the bearing becomes loose, and eccentricity of the seal or contact between the rotating parts and fixed parts may cause vibration, leakage, etc., leading to bearing damage or shaft breakage in some cases.
We can perform weld overlay repair of shafts at the site of installation, cutting, assembly, and testing, making full use of our maintenance technology and equipment that we have cultivated over many years.
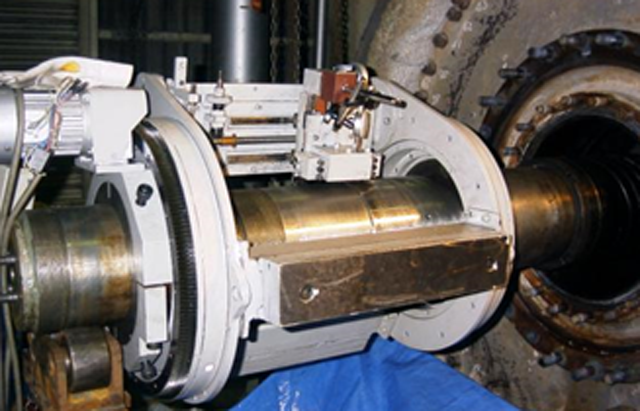
1. Repair details
- (1) Care of damaged parts
- (2) Welding and plating
- (3) Shaft surface machining (machining to specified tolerance and finishing accuracy)
- (4) Assembly and rotation test
2. Advantages
- (1) Repair work is performed on-site, so there is no need to take the shaft outside and no transportation costs to the factory.
- (2) Repair period can be shortened because there is no need to carry out and transport the shaft.
Flange On-Site Repair
Leakage from flanges, if left unchecked, can lead to serious accidents.
After years of use, the seat surface of the flange can become distorted and deformed due to corrosion, resulting in leakage.
We can perform on-site repairs such as weld overlay, lining, etc., as well as seal surface cutting, assembly, and testing while the equipment is still installed, making full use of the maintenance technology and equipment we have cultivated over many years.
We can also perform repair work on the installation surfaces of motors, reduction gears, and other equipment, as well as on the surfaces of structures.
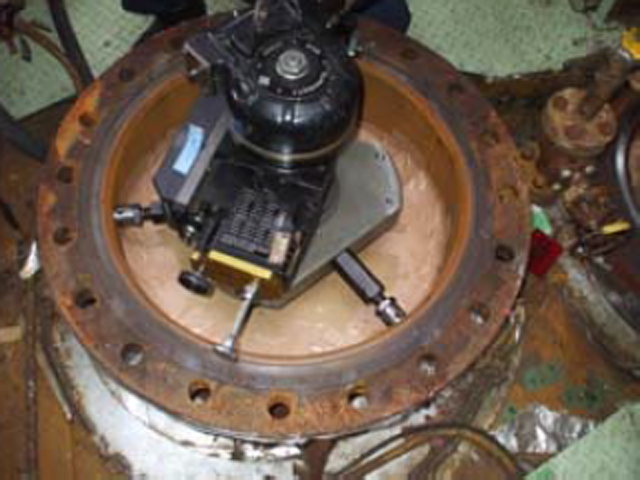
1. Repair details
- (1) Removal of defective parts
- (2) Weld overlay
- (3) Seat face cutting (various shapes of seat faces)
- (4) Assembly and leak inspection
2. Advantages
- (1) Repair work is performed on site, so there is no need to take the equipment outside and no transportation costs to send the equipment to an outside factory.
- (2) Repair period can be shortened because there is no need to carry out and transport the equipment.
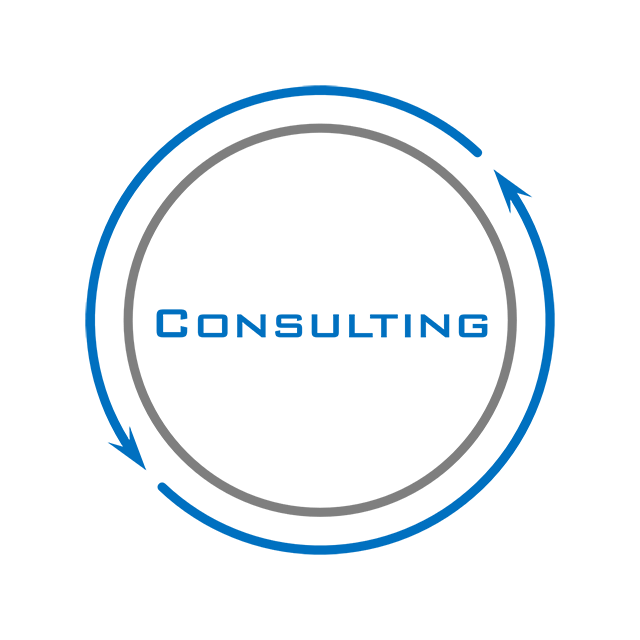
Consulting Service
- Maximizing your equipment performance -
Inspection of Agitators and Agitation Tanks
Agitation tanks are operated in a harsh environment with repeated pressure and temperature changes, corrosion, and vibration of the rotating parts.
Long-term operation may cause material deterioration in parts that are not visible on the surface and functional deterioration of the structure (loosening, leaks).
For stable long-term operation, we recommend that the planning a comprehensive inspection and maintenance before any major problems occur.
In this case, please contact our company, which has abundant knowledge and experience.
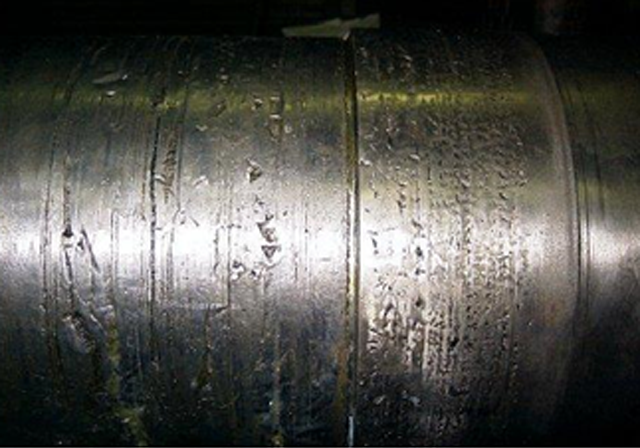
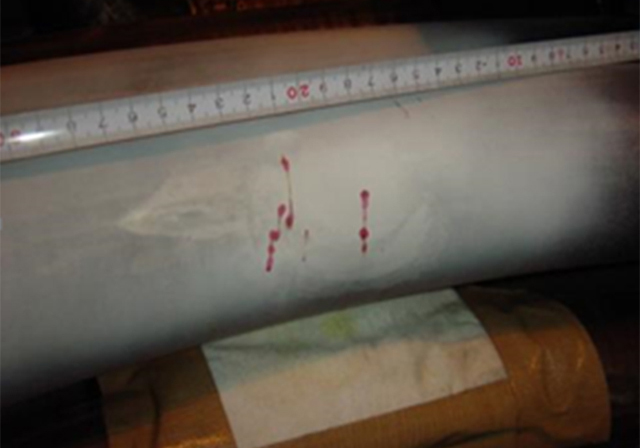
<Main inspection details>
- (1) Agitation system: Inspection of the shaft seal and drive unit, replacement of parts, and diagnosis of the degraded shaft and blades.
- (2) Agitation tank system: Diagnosis of deterioration of the walls of the main body, diagnosis of deterioration of equipment inside the can, inspection and maintenance.
- (3) Others: Inspection and maintenance of flange seat surface, seat, parts outside the can, and related equipment.
Agitator repair and improvement
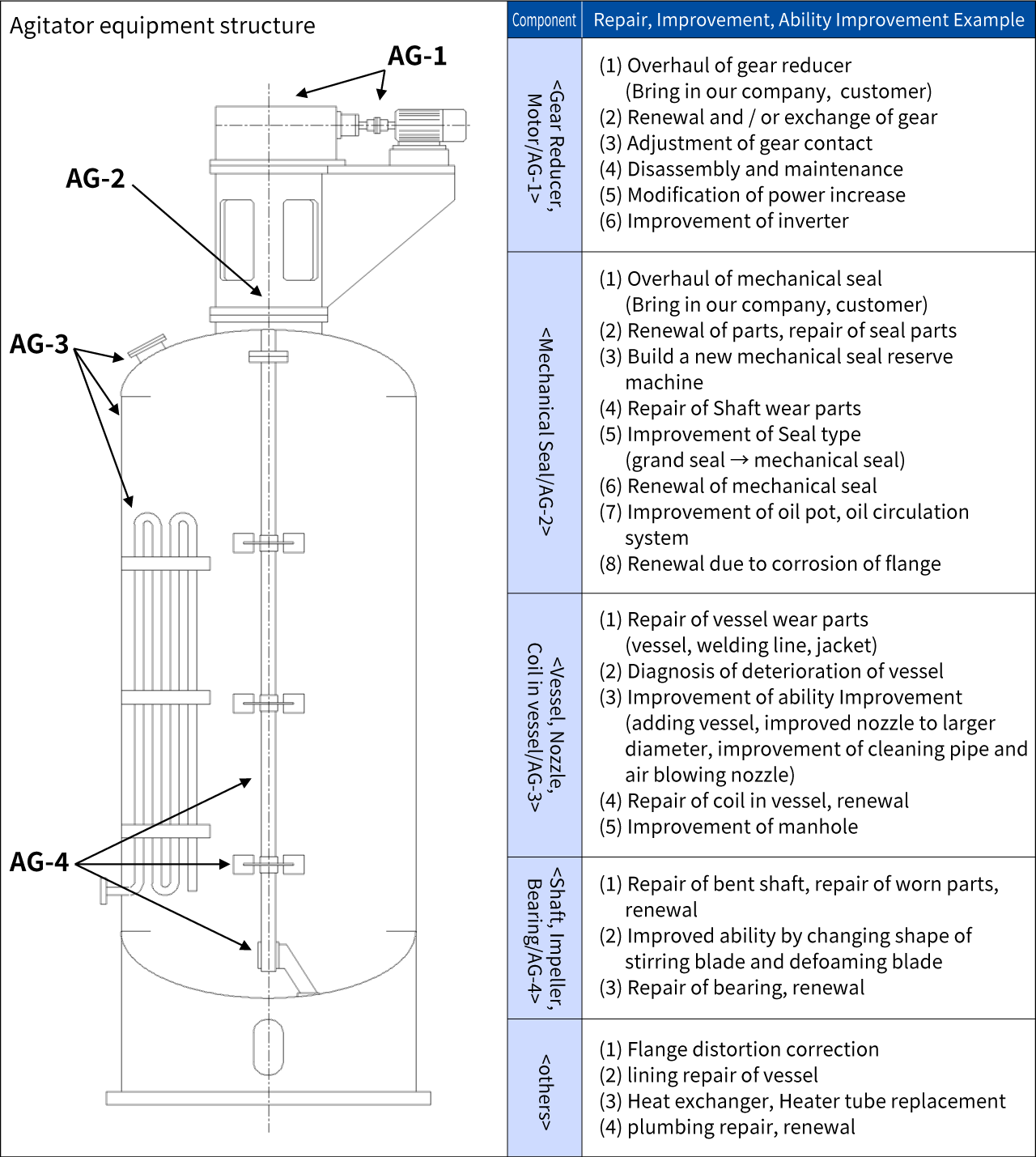
Service recommendation map
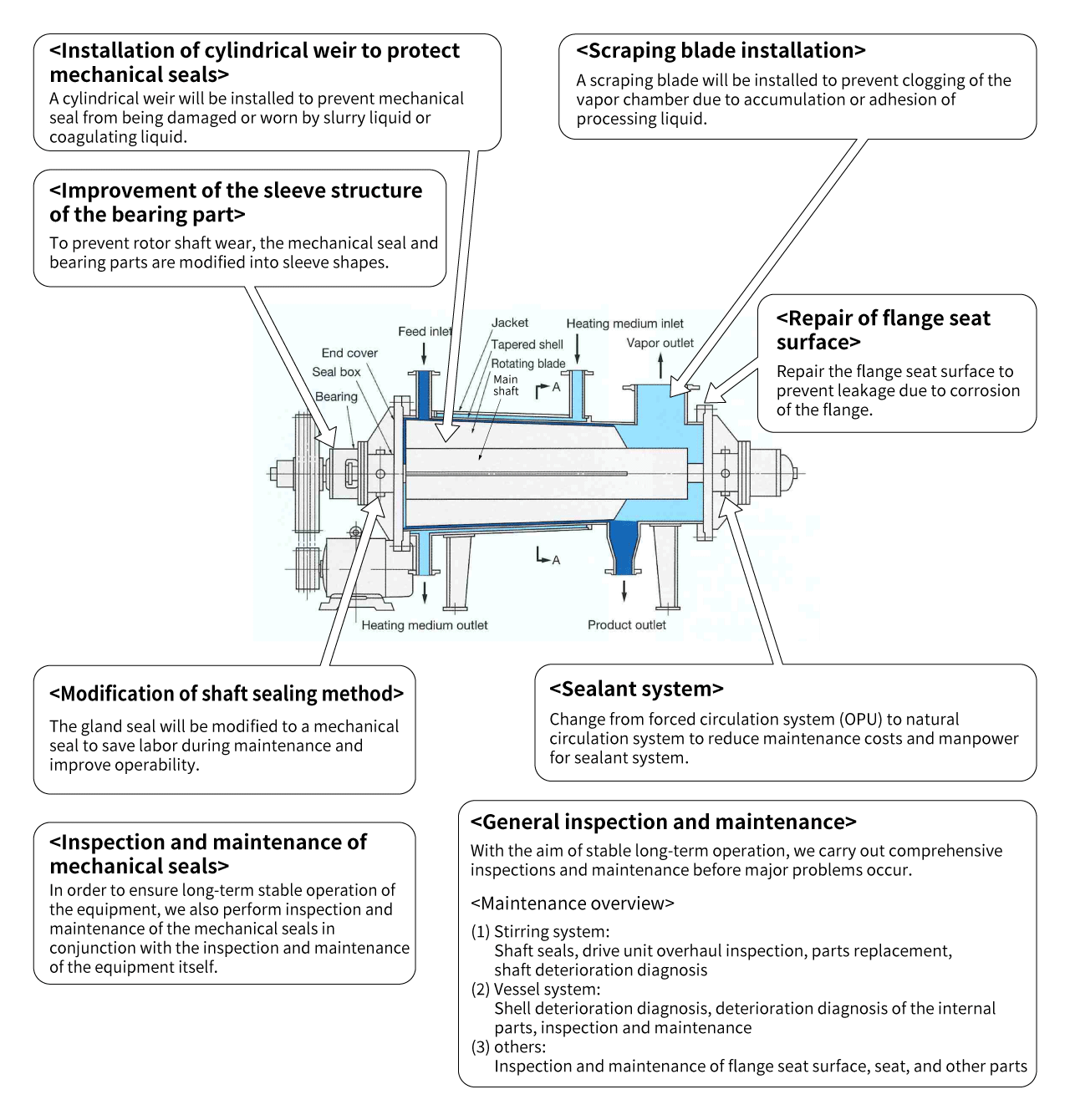
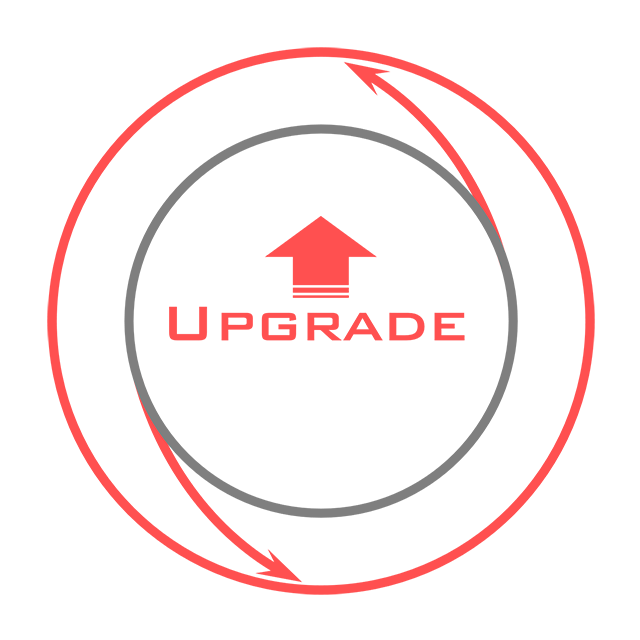
Upgrade Service
- Further expanding the capabilities of your equipment -
High efficiency
- Agitator blade shape modification
We work with agitator manufacturers to conduct flow analysis and laboratory experiments to propose optimal blade shapes.
Energy saving
- Motor inverter conversion
Inverterization allows operation at optimum rotation speed, resulting in energy savings.
Longer service life, lower maintenance costs, stable operation
- Shaft wear countermeasures
- Installation of additional sleeves
- Installation of intermediate coupling
- Conversion from gland packing or V-packing to mechanical seal
- Addition of surface hardening treatment (plating, coating, quenching, nitriding, etc.)
- Mechanical seal
- Modification of sealant system
Maintenance cost reduction by changing from forced circulation system to natural circulation system - Addition of cylindrical weir
Weirs are added to prevent wear and tear due to intrusion of process fluid, extending service life.
- Modification of sealant system
- Gear coupling
- Modification to universal joint
Reduction of centering time
- Modification to universal joint
- Reduction gear
- Conversion to inverter In addition to energy-saving effects, reduction of reduction gear maintenance costs
- V-belt
- Reduction in the number of belts by changing the V-belt shape
Easier V-belt replacement and V-pulley replacement
- Reduction in the number of belts by changing the V-belt shape
- In-can coil
- Renewal of coils with increased capacity
Reduction of coil load prevents contamination due to coil cracking and stabilizes operation
- Renewal of coils with increased capacity
- Measures against internal adhesion
- Addition of a scraping device to reduce cleaning frequency and extend operation time