Extrusion Presses
In addition to machine installation and service, our mission is to meet a wide range of customer needs, including modifications and renewals that contribute to environmental improvement, cost reduction, productivity improvement, and quality improvement, as well as relocation of production equipment in accordance with the optimization of production facilities.
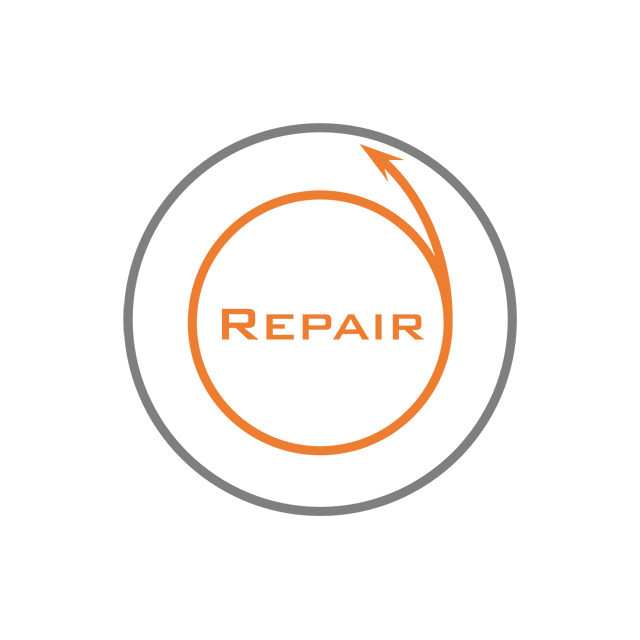
Repair Service
- Restoring your equipment to its original performance -
Preventive maintenance
Replacement of packings and seal kits
Regular replacement is recommended to prevent oil leaks.
- Main cylinder
- Side cylinder
- Container cylinder
- Shear cyllinder
- Prefill valve cylinder
- Special cylinder
Replacement of consumable parts
Regular replacement is recommended to maintain machine accuracy.
- Machine base liner
- Slide shoe
- Die slide liner
- End platen liner
- Main shear liner
- Billet loader bush
- End platen pressure ring
- Main cross head pressure ring
Elocation
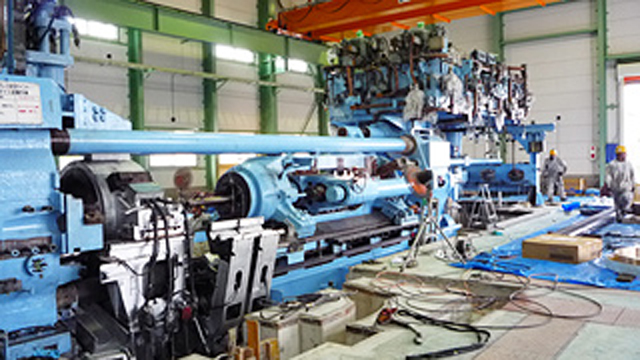
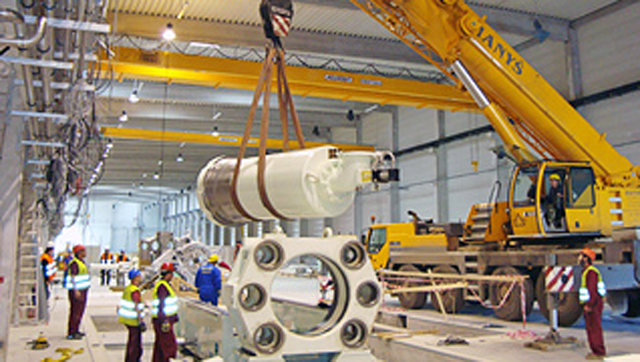
Overhaul, dismantle, transport, install and relocate shut-down extrusion equipment.
For overseas relocations, we support our customers to resume production immediately after the relocation in collaboration with our overseas service centres.
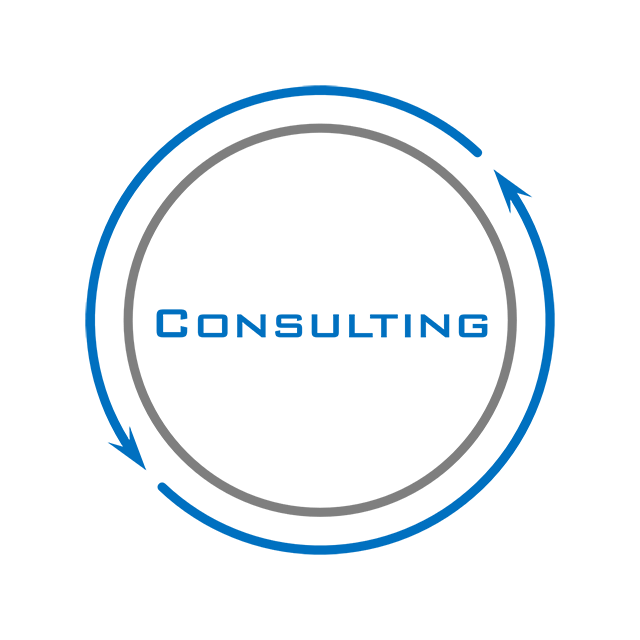
Consulting Service
- Maximizing your equipment performance -
Increased productivity through reduced idle time
Reduced idle time
The objective is to reduce idle time and improve productivity of extrusion presses that have been installed for more than six years.
Proposal details
Adjustment of hydraulic valves and other components of existing equipment and review of electrical sequencing and amplifier adjustments.
Target value: 2 seconds less than current idle time
Construction schedule
Dispatch one mechanical and one electrical SV each.
One unit per day, adjusting idle time for production conditions.
Equipment Diagnosis
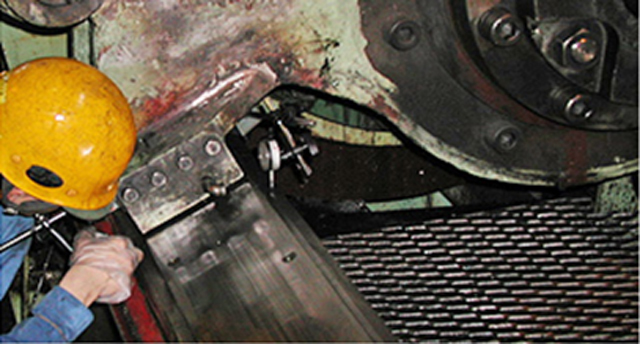
Preventive maintenance
- Non-destructive testing of key parts
- Main cylinder vertical degree, machine base horizontal degree
- Operational condition checks
- weld repair
Check hydraulic system
- Cylinder oil leakage inspection
- Pressure testing of relief valves.
- Cleaning of oil cooler
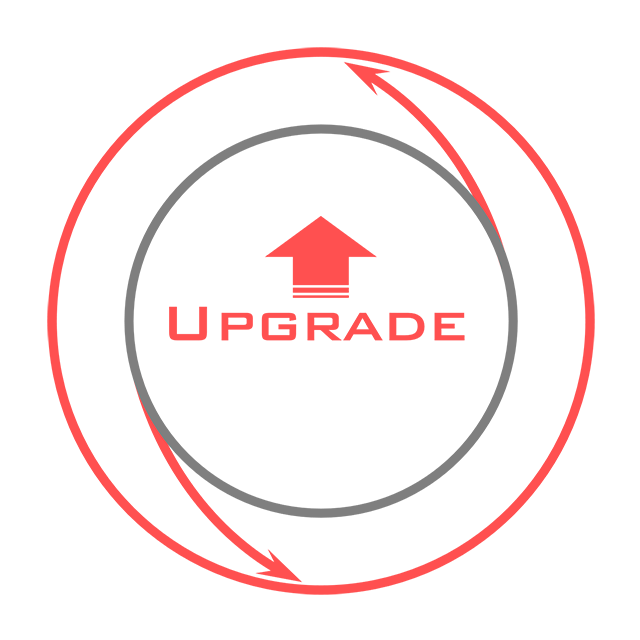
Upgrade Service
- Further expanding the capabilities of your equipment -
Conversion of the main relief valve to a logic valve.
1. Objectives
Reduced time for one extrusion cycle
2. Structural overview
The relief valve maintains the pressure balance at the actual operating pressure in relation to the set pressure, with hydraulic oil escaping from the valve in proportion to that pressure.
The balanced piston type relief valve used on older presses is replaced by a logic valve type to reduce the amount of hydraulic oil escaping.This reduces the start-up and initial speed time at the start of the extrusion process, thereby reducing the extrusion time per cycle.
3. Effects
At pressures of 180 kg/cm2 or more at the start of extrusion, 1800 T has the effect of reducing costs by approximately 1 million yen per year.The amount of oil escaping from the relief valve is reduced and the temperature rise of the hydraulic oil is reduced.
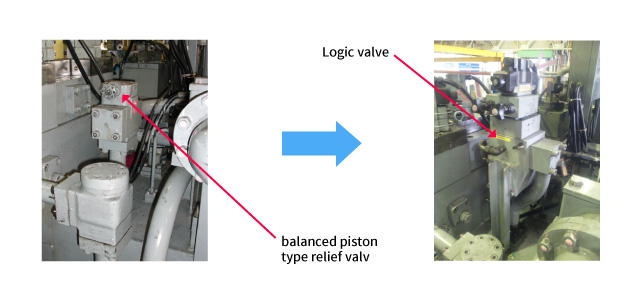
Die cassette locking device installed.
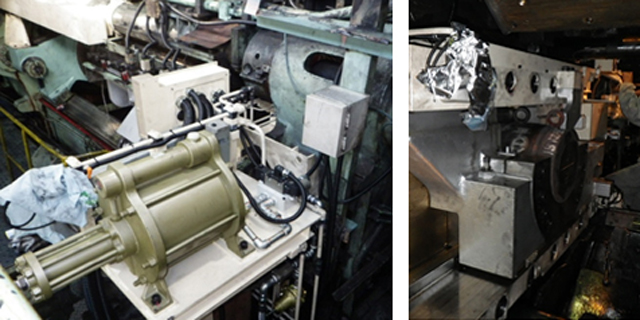
1. Objectives
Improved quality, uniform butt cutting surface
2. Structural overview
Hydraulic cylinders are installed at the top and bottom of the die cassette to push the die cassette towards the platen, enabling the die to be locked.
The main shear locks the die during butt cutting, reducing movement in the die cassette and ensuring an even cut surface.
- Retrofit existing dicassettes.
- Use units that change from pneumatic to hydraulic pressure with an air hydro booster.
3. Effects
Improved cutting reduces aluminium foil adhesion to the die, resulting in fewer aluminium foil roll-in defects in the extruded product.Improved container sealing reduces aluminium blooming defects.
Energy-saving operation of cooler pumps with inverters
- The motor speed can be varied according to the oil noise or the motor can be stopped.
- Existing motors can be diverted by fitting inverter surge suppression filters as required.
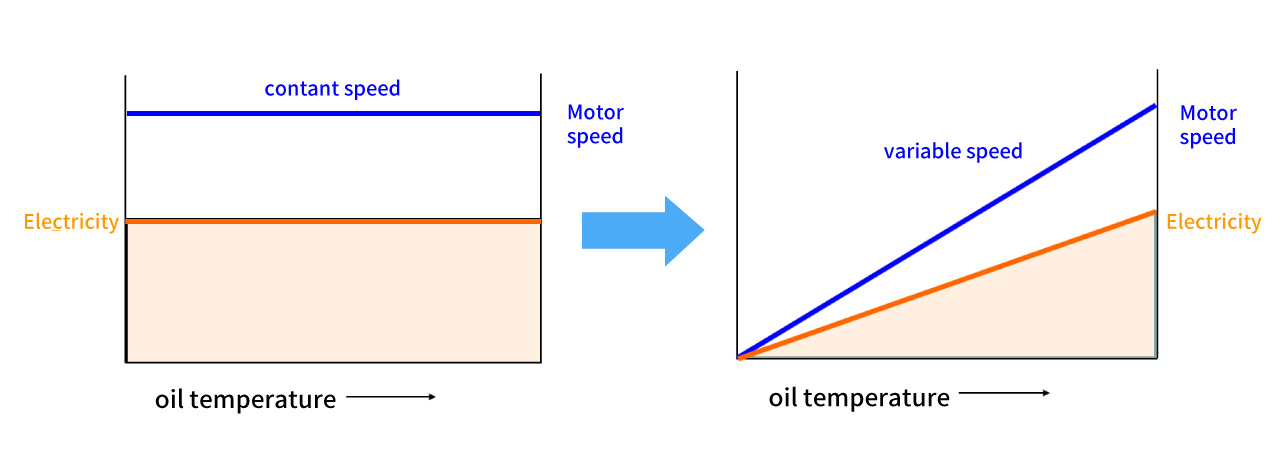
Billet temperature measurement
1. Objectives
In extruded products, billet temperature is important for quality control, and tapered heating is particularly effective in ensuring uniform product temperature, which has a significant impact on quality.
2. Function
- Inspection sensors such as thermocouples cannot detect temperature distribution in the longitudinal direction, but radiation thermometers can be used to measure temperature distribution in the longitudinal direction.
- The measured data is displayed on a waveform display on the touch screen increase, allowing the user to check heating temperatures and taper trends.
- Upper and lower limit settings allow detection above the temperature.
- Waveform data can be stored on SD cards.
3. Effects
- Billet temperature distribution can be checked.
- It can be used as a traceability tool.
- Temperature anomalies can be monitored.