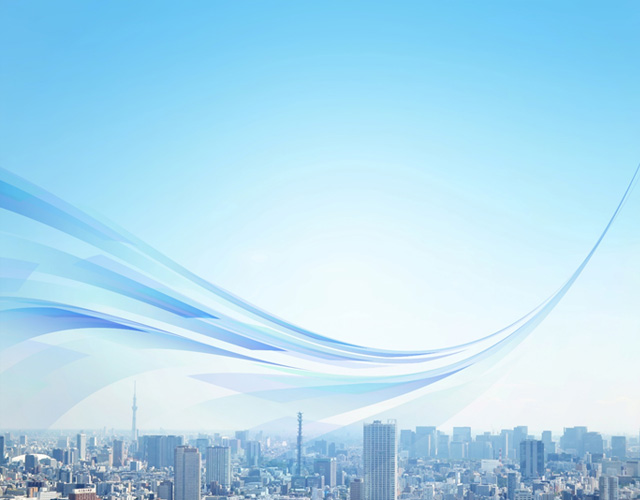
UBE Machinery's Injection Molding
“Lightweighting Technology”
Lightweighting is an important issue that is essential for carbon neutrality and cost reduction. To meet these needs, UBE Machinery has developed high-quality foam molding and composite molding technologies by concentrating its technological capabilities.
Injection Foam Molding
To ensure both rigidity and impact resistance of molded products and weight reduction, expansion of the foam layer and miniaturization of the foam size are required, and highly responsive and precise control of the mold opening and closing motion (core back) is an important key technology for consistent, high-quality foam molding.
UBE Machinery supports customers' product development and stable production with the industry's most extensive track record and experienced molding technology in injection foam molding, which realizes lighter and more functional products.
DIEPREST
DIEPREST, an ultra-precise mold open/close control system, enables core-back foam molding to reduce the weight of plastic products such as automobile interior parts and to achieve uniformly fine foaming.
Core-back foam molding
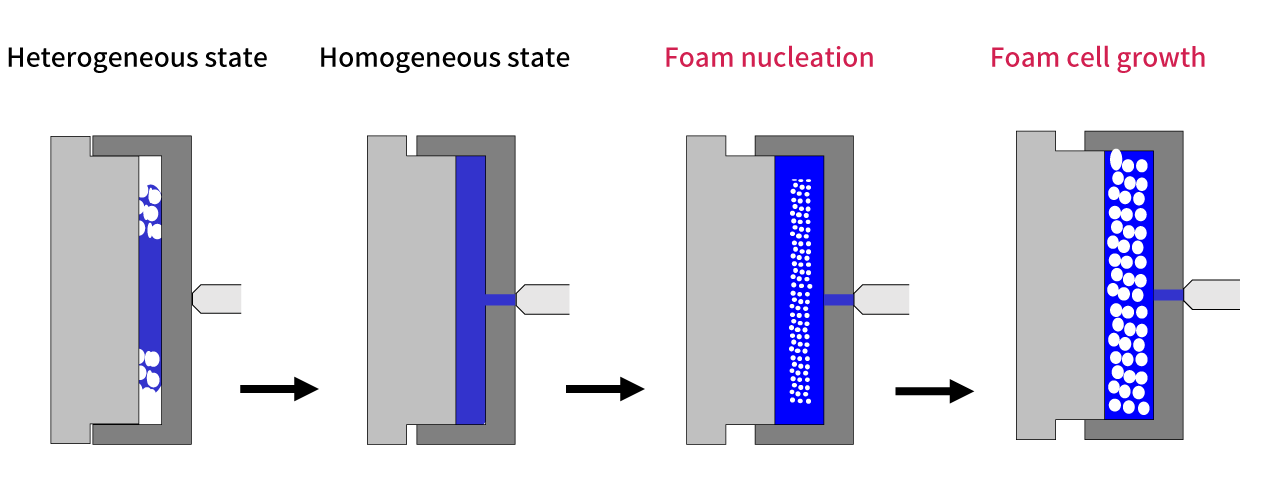
*MuCell® is a registered trademark of TREXEL,Inc.
MuCell® molding is a foaming technology that uses supercritical gas (SCF) to generate microcells (microbubbles) inside molded products. The supercritical action allows a large amount of foaming gas to dissolve into the resin, resulting in greater weight reduction, improved flowability, and better deformation resistance.
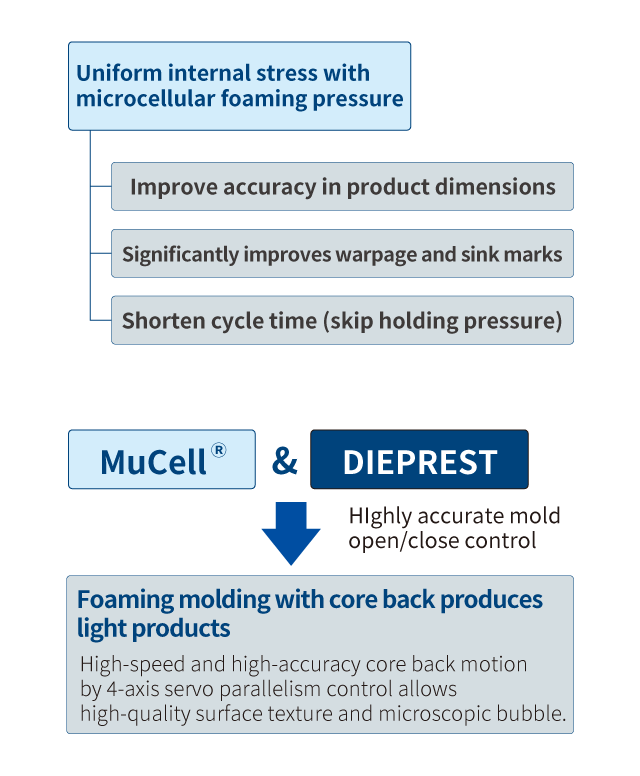
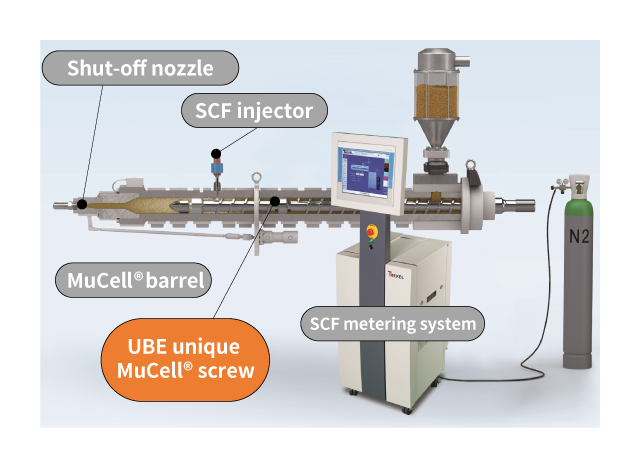
Fiber Reinforced Composite Molding
In response to the growing need for lighter weight products, such as electrification of automobiles, UBE Machinery offers a lineup of optimal screws to solve the problem of "ensuring high strength and high rigidity of products" in LFT injection molding. In addition, we have developed the "DLFT Molding System," which enables the reduction of raw material costs through its advanced technological capabilities, and is responding to a wide range of molding technology establishment.
*LFT: Long-fiber-reinforced thermoplastic
LFT SCREW
This screw is specially designed for reinforced materials containing glass and carbon long fibers.
Fiber breakage during plasticization is reduced, and the high physical properties of long fiber materials can be realized in products.
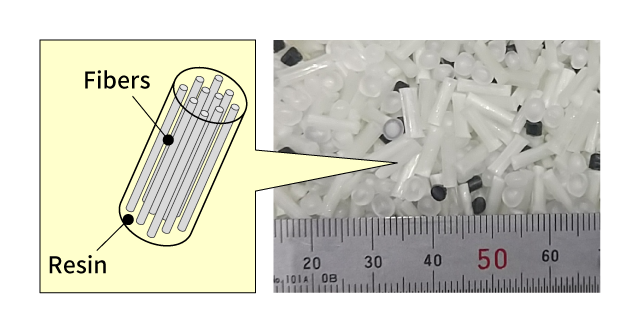
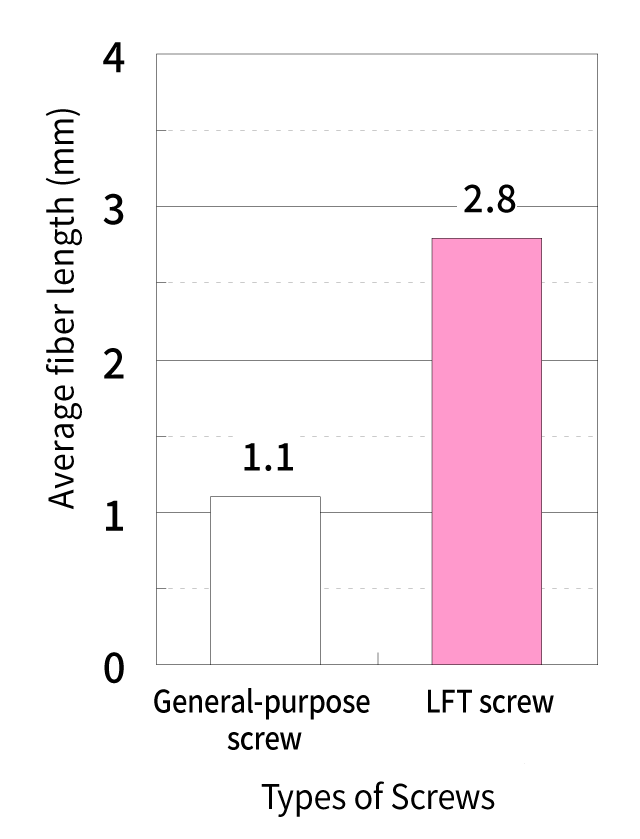
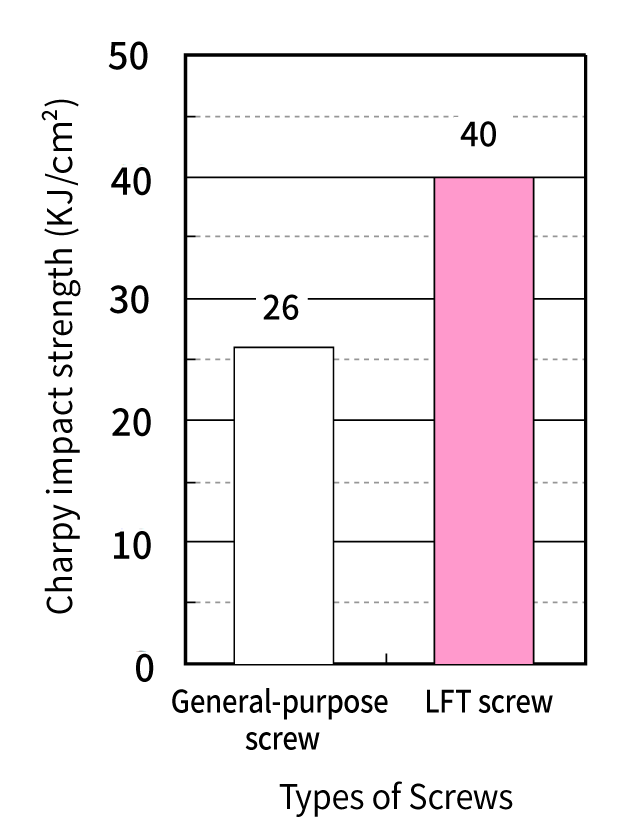
DLFT System (Injection molding system with direct compounding of long fiber)
DLFT System is a technology that contributes to material cost reduction by directly feeding chopped fiber bundles into an injection molding machine. Lightweight and high-strength LFT products can be molded at low cost.
DLFT System: Registered trademark of UBE Machinery in Japan
What is DLFT?
- Simple structure with inline screw system, yet achieves the required plasticizing capacity, fiber length, and fiber dispersion.
- Simple structure for easy operation and maintenance.
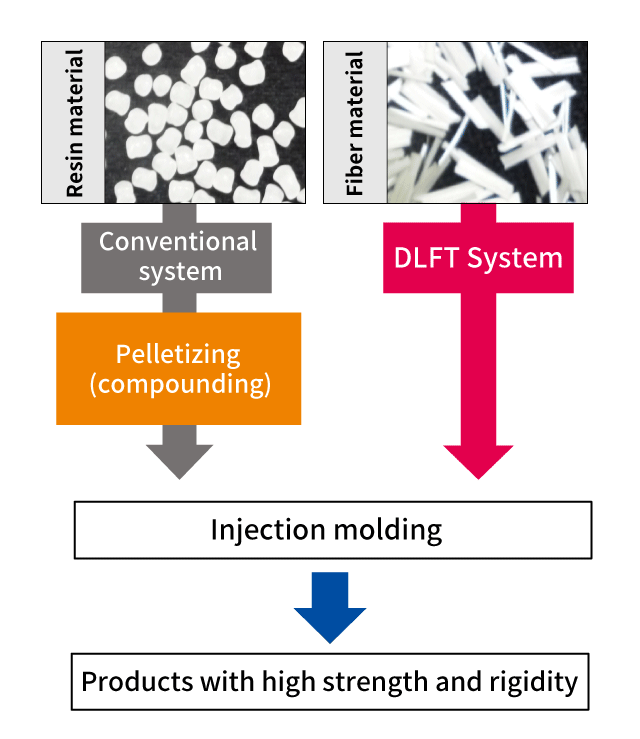
DLFT System Configuration
- Resin and fiber materials are directly (compound-less) fed into the injection molding machine to form lightweight, high-strength LFT products.
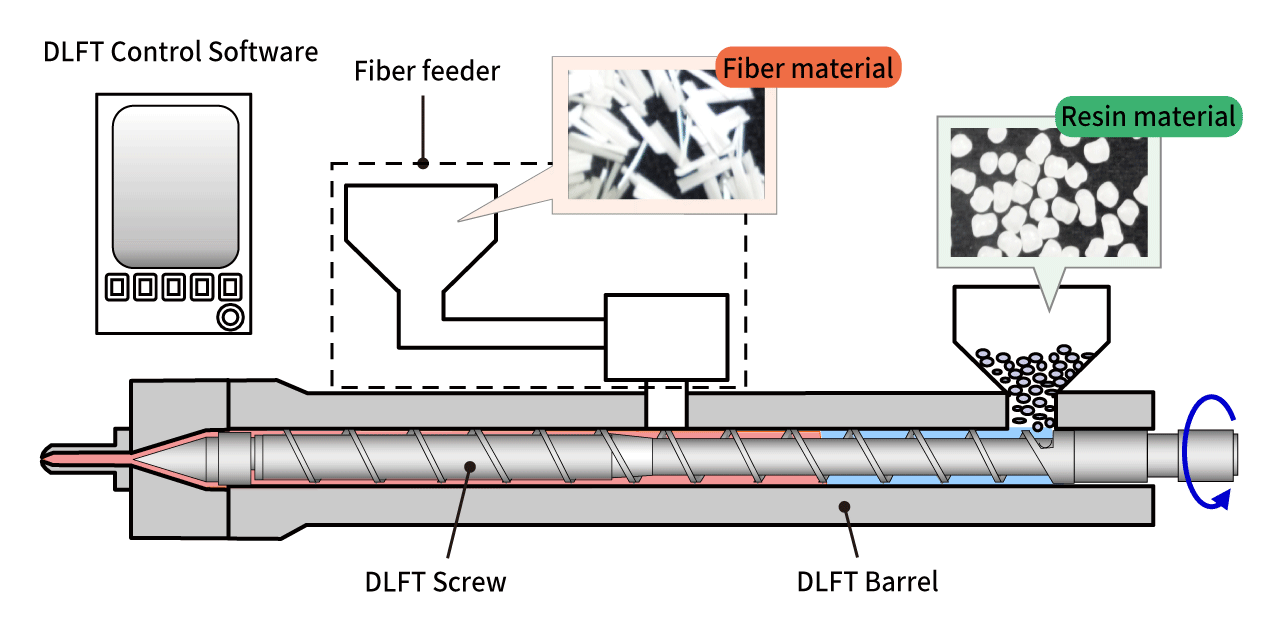
About DLFT System