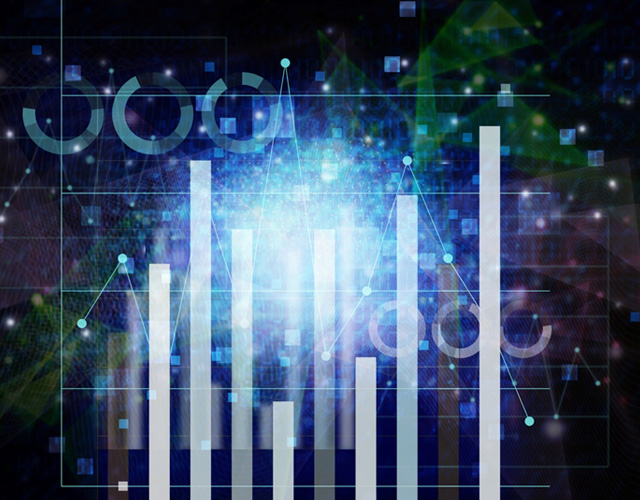
UBE Machinery's Injection Molding
“High-Cycle Molding Technology”
We offer total technology proposals from the entire molding environment, including analysis of actual production conditions and approaches to development goals. Please also use our trial facility to quantitatively evaluate the effect of our proposed technology on actual production.
High-Cycle Performance of Electric Injection Molding Machines
In addition to a high injection rate, electric injection molding machines can significantly shorten the cycle time compared to hydraulic injection molding machines because they are equipped as standard with simultaneous operation, which is not easy with hydraulic injection molding machines, and high-precision position control using servomotors to minimize the low-speed section in variable speeds, which is necessary.
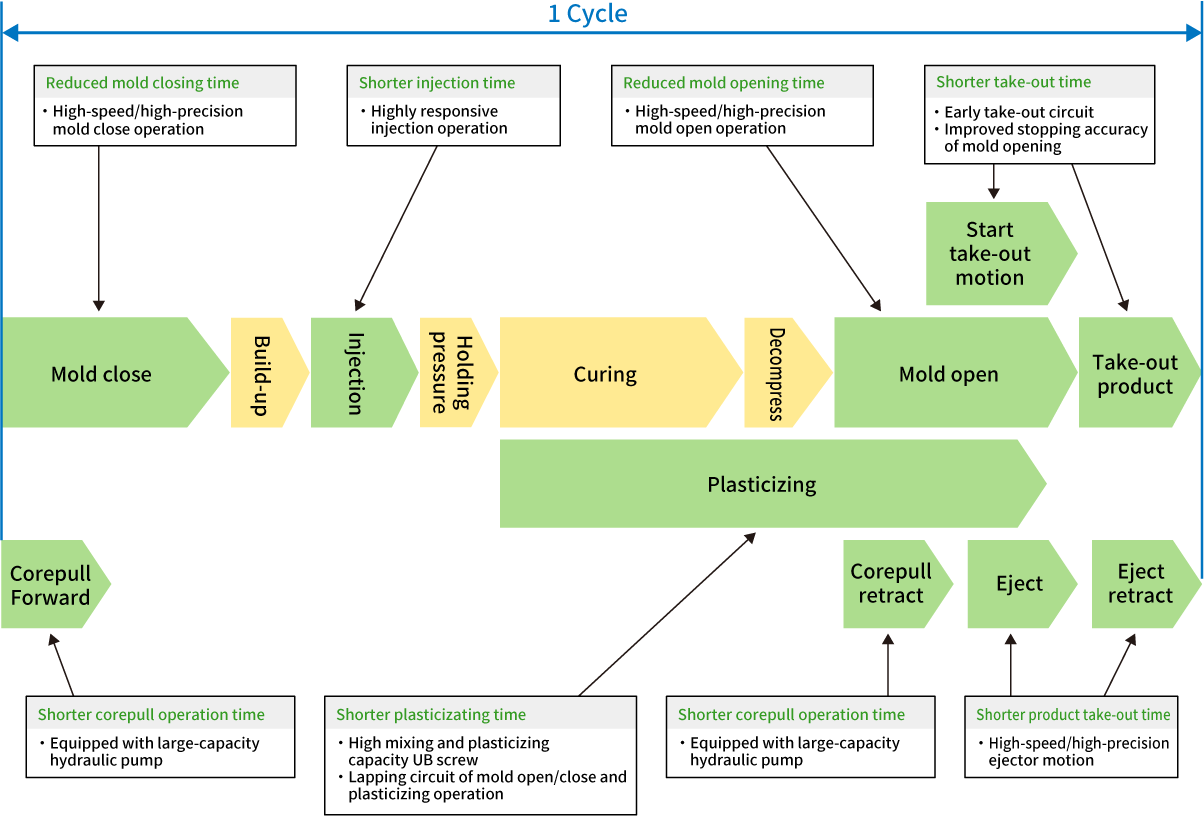
"What moves is light and fast!"
UBE Machinery's toggle-type all-electric injection molding machines
UF Series, HH Series
UBE Machinery's UF and HH series toggle-type all-electric injection molding machines realize high-cycle molding with compact and quick operation by combining high-response, high-speed injection with a high-rigidity, high-speed mold clamping device and optimizing the toggle link mechanism to reduce ball screw strokes.
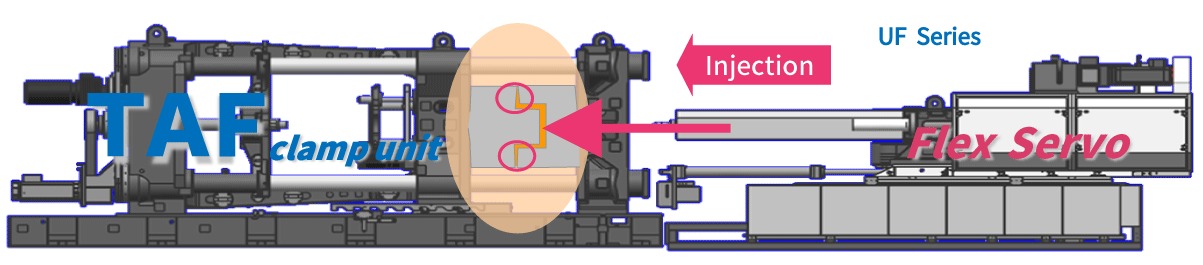
UBE Machinery's 2-Platen Electric Injection Molding Machine with Even Higher Cycle
em III series
In the “em III” series, the mold release action, which was performed by the mold clamping cylinder, is driven at high speed by the mold opening/closing ball screw (servo mold release), thereby increasing the mold opening/closing speed and achieving even higher cycle time than our conventional machines.
Servo-Hydraulic Injection Molding Machine with High Cycle
MMX Series
Equipped with Molding Time Reduction Functions for High-Cycle Molding Operation as Standard
UBE Machinery's MMX series servo-hydraulic injection molding machines are equipped with various molding time reduction functions as standard, contributing to customers' productivity improvement through high-cycle molding operation.
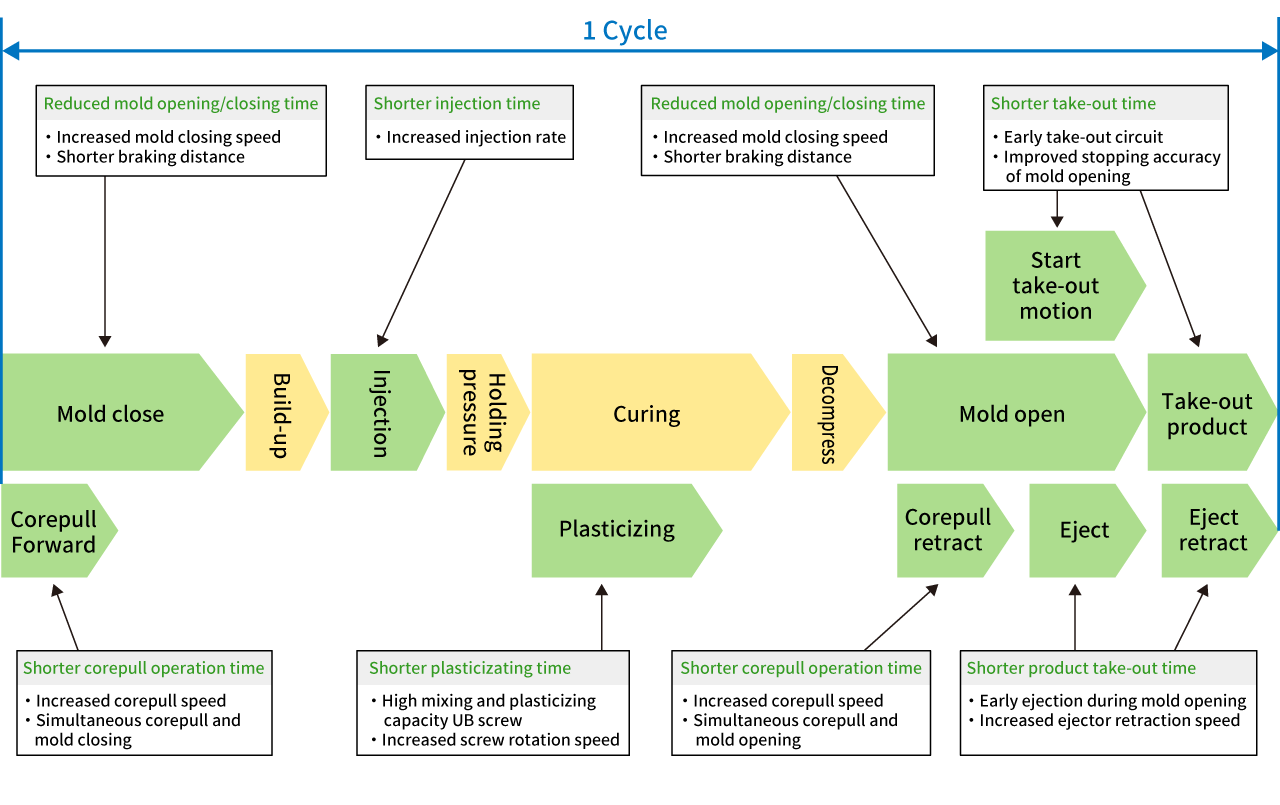
Increased Plasticizing Capacity (Screw Technology)
We propose screws that maximize performance according to the molding environment, from general molding to special molding, based on our abundant screw variations and plasticizing characteristic analysis technology developed by combining our long-accumulated technology and experience.
Plasticizing Electrification
(Compatible with hydraulic machines MMV and MMX series)
Measuring time can be shortened by using a plasticizing drive configuration (increased screw rpm) suitable for the plasticizing power of the current material used. In addition, when used in combination with a shut-off valve, plasticizing can be performed in parallel with other processes (Lapping operation of plasticizing process and mold opening/closing process), thereby shortening the cycle time for production where measuring time is a bottleneck.
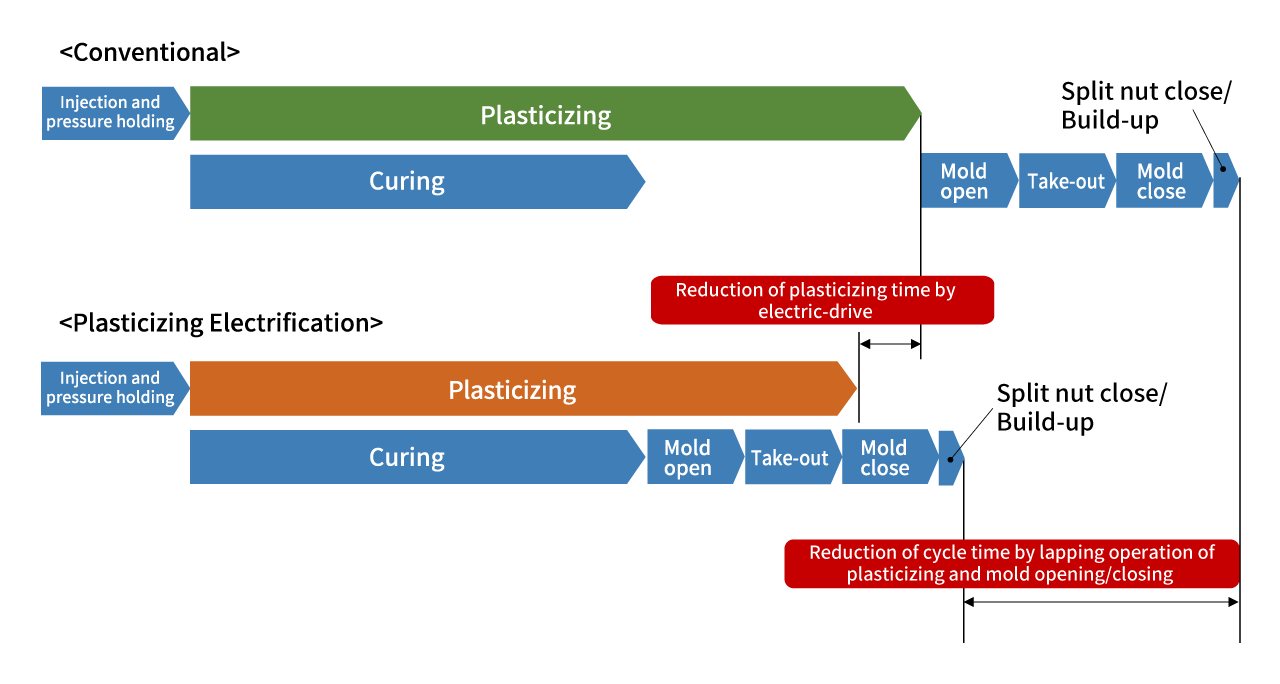
Product Consolidation (SCS Molding)
This is a molding method in which multiple product groups are molded on a single molding machine. By using a single molding machine to mold different products that were previously produced using multiple molding machines, the total tact time for a set of products can be reduced.
*SCS: Sequential Cavity Separation
Shorter cooling time (AIRPREST)
By precisely controlling the mold clamping force in multiple steps according to the in-mold filling condition during injection filling, gas degassing from the PL(parting line) surface of the mold is promoted to reduce local heat generation due to adiabatic compression of gas in the cavity, and the effect of uniforming and lowering the product surface temperature makes it possible to shorten cooling time.
*AIRPREST: Registered trademark of UBE Machinery in Japan
Comparison of surface temperatures
Normal molding
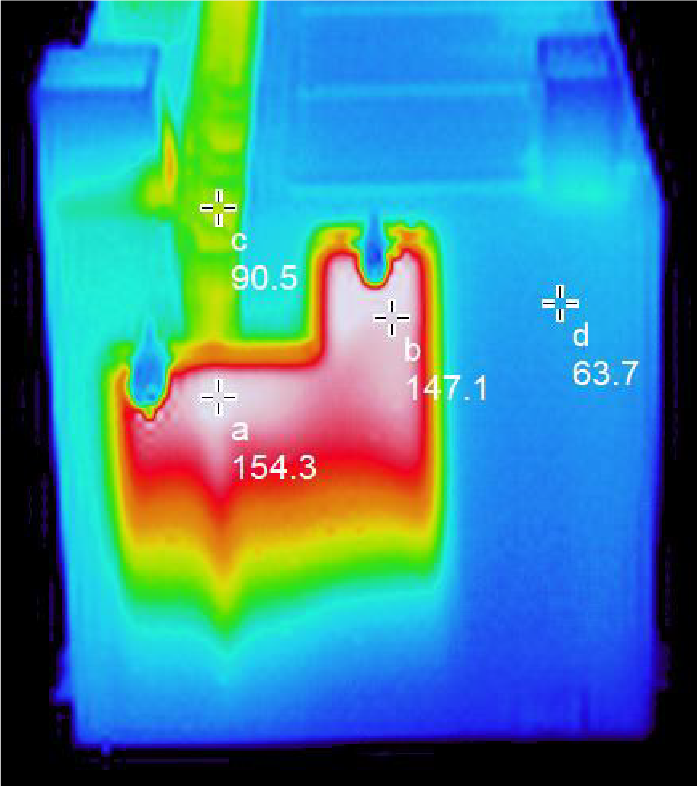
AIRPREST molding
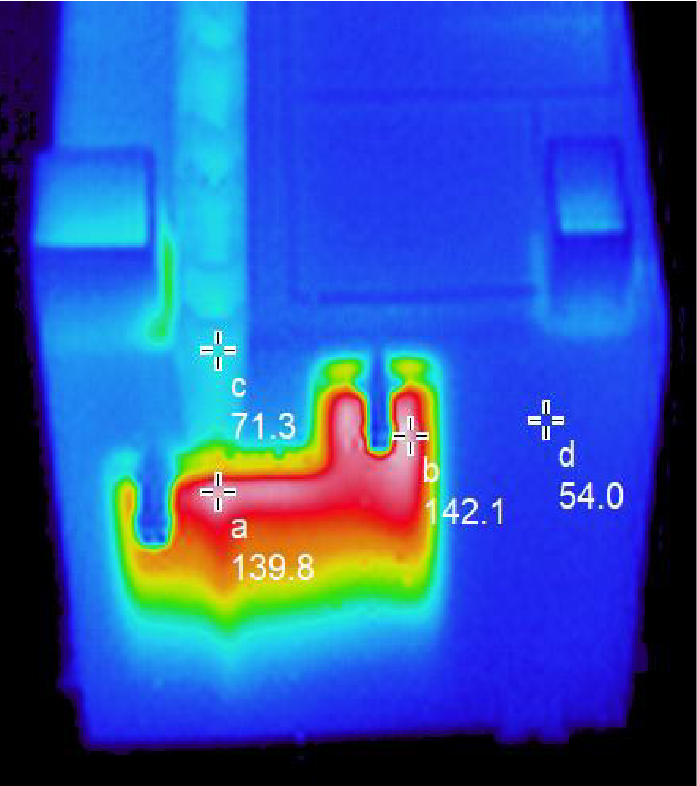
Measuring point | Normal molding °C | AIRPREST °C |
a | 154.3 | 139.8 |
b | 147.1 | 142.1 |
c | 90.5 | 71.3 |
d | 63.7 | 54.0 |
- Shorter cooling time (shorter cycle time)!
- Reduction of defect rate due to smaller deformation after demolding!
- Easier post-processing (ex. attachment of container lid)!
Other effects such as reduction of mold clamping force have been achieved.