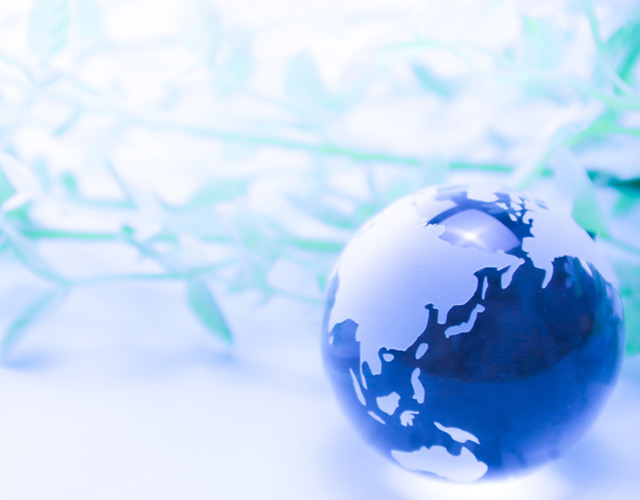
UBE Machinery's Injection Molding
“Technology Contributing to
Carbon Neutrality”
Carbon neutrality is the equilibrium between greenhouse gas emissions and absorption. To achieve this goal, it is necessary to conserve and enhance the reduction and absorption of carbon dioxide (CO2) and other greenhouse gas emissions. UBE Machinery's electric and servo-hydraulic injection molding machines are highly energy-efficient machines that have been developed through years of technological innovation to reduce CO2 emissions during operation, contributing to carbon neutrality.
Customer Needs |
UBE Machinery's Solutions | |||||||||
---|---|---|---|---|---|---|---|---|---|---|
Supported Technologies |
Equipment Technology | Plasticization system |
Mold clamping control | Injection control |
||||||
Heater temp. control |
Power Regeneration System |
Pump Control |
Upgrade | Screws RELATED. |
Toggle Electric |
2-Platen Electric |
DIEPREST | SCS | ||
Electric Drive | Drive Control | ● | ● | ● | ||||||
Downsizing of machine |
Low pressure injection Low clamping force |
● | ||||||||
Equipment consolidation |
Integrated molding | ● | ||||||||
Production Power Reduction |
Barrel Temp. Rising Efficiency |
● | ||||||||
Melt Optimization Screw Shape |
● | |||||||||
Power Reuse | Power Recovery | ● | ||||||||
Energy-saving improvement |
Suggestions for Improvement |
● |
Energy-Saving Performance of Electric Injection Molding Machines
Electric injection molding machines save much more energy than hydraulic injection molding machines due to the difference in power transmission efficiency and the fact that the motor is driven only for necessary operations. Other energy-saving effects include economic and environmental improvements due to a significant reduction in hydraulic oil consumption, economic improvements due to a significant reduction in cooling water, productivity improvements due to high-cycle molding, and reduction of "wasted" shots by stabilizing molding quality.
(Note) The energy-saving effects (shown below or above) vary depending on the shape of the molded product, resin, and molding conditions used by the customer. Please consult with us about the energy-saving effects that can be expected from your injection molding machine.
UBE Machinery's Toggle Type All Electric Injection Molding Machine with Outstanding Energy Saving Performance
UF Series, HH Series
UBE Machinery's UF and HH series toggle-type all-electric injection molding machines are all-electric machines that do not require electric power to maintain the clamping force, taking advantage of the toggle-type mold clamping mechanism, and offer outstanding energy-saving performance by significantly reducing energy consumption compared to hydraulic injection molding machines.
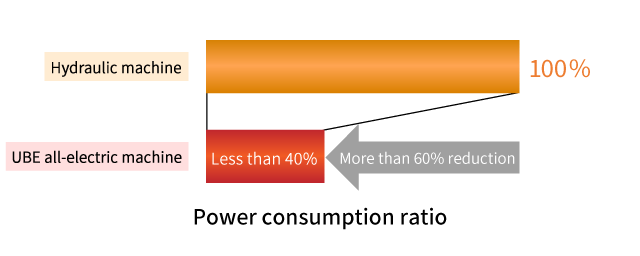
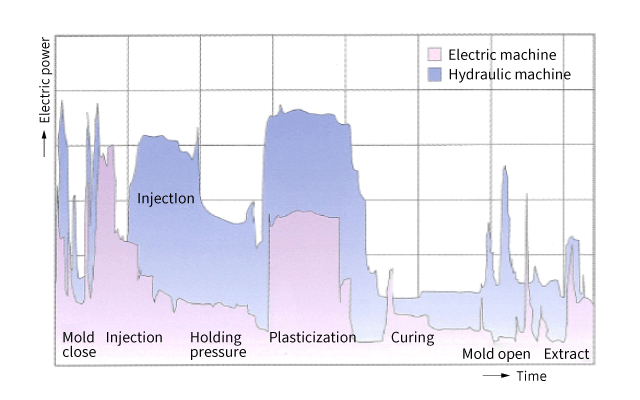
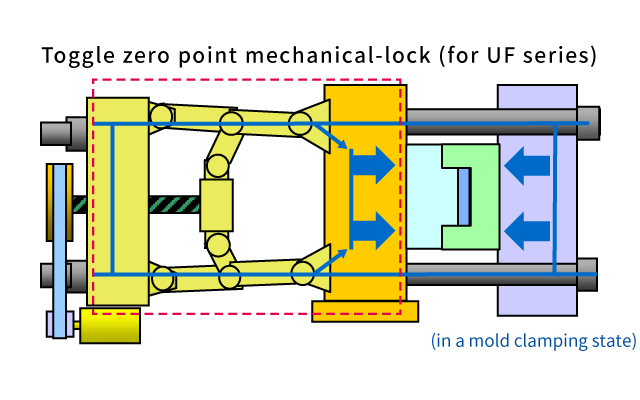
Mold close + Build-up, Decompression + Mold open require drive power
Further Energy Savings on UBE Machinery's 2-Platen Electric Injection Molding Machines
em III Series
UBE Machinery's 2-platen electric injection molding machine, em III series has further improved the pressure holding performance of the hydraulic system to significantly reduce energy consumption during mold clamping pressurizing, holding, and decompressing, which has been a problem for 2-platen electric injection molding machines, and has achieved energy-saving performance equivalent to that of toggle-type all-electric injection molding machines.
Power consumption ratio of 1300t class (compared to our machines)
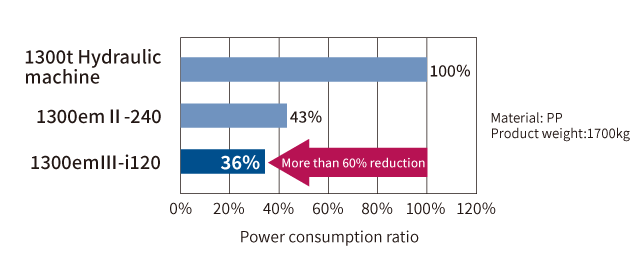

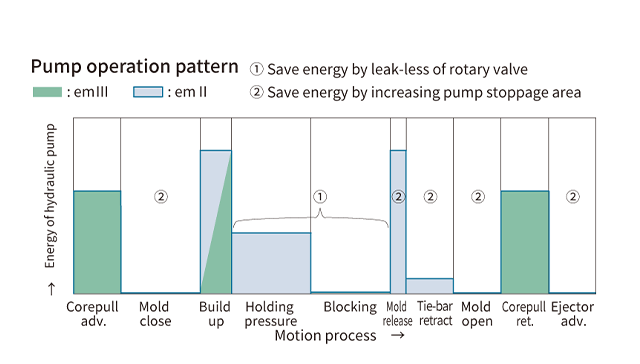
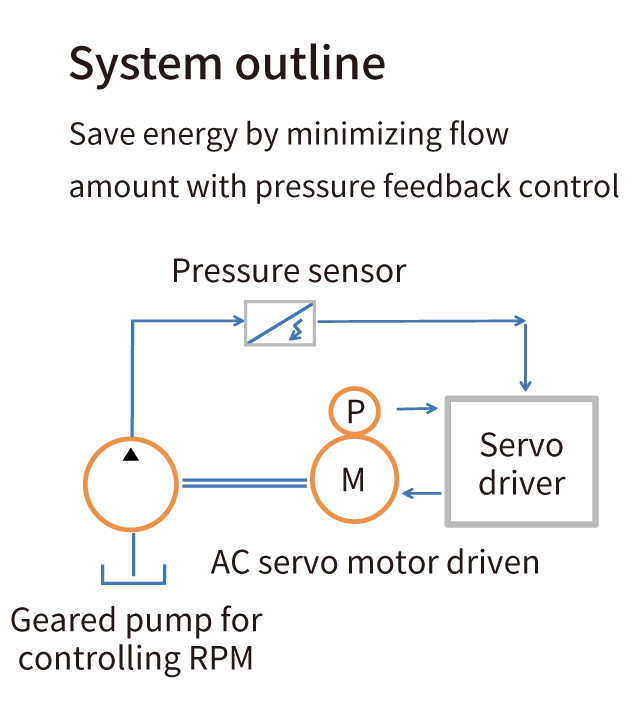
“Eco Barrel Cover” (Option) reduces heater power consumption
“Plasticizing” and “Heater” operation processes account for a large percentage of the power consumption of a molding machine. The "Eco Barrel Cover" (Barrel Heater Heat Insulation Cover) reduces the heat dissipation from the injection molding machine barrel to the atmosphere and improves energy efficiency when the barrel temperaturerises. This functional cover is custom-made by UBE Machinery with excellent safety, durability, and energy efficiency.
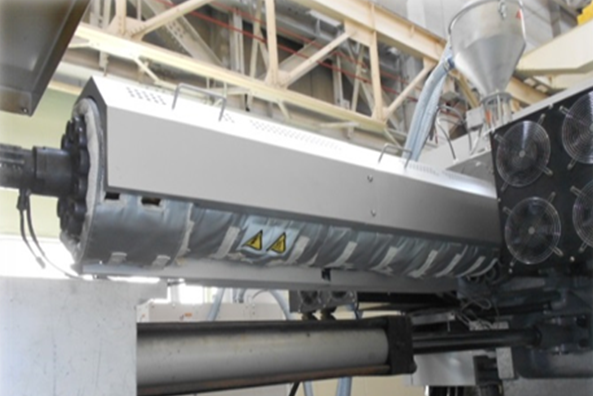
- Temperature stabilization by highly insulated materials
- Heater power reduced by 20% or more
- Reduced environmental impact
Example of power saving cost estimation
Power consumption data for a 1050-ton class clamping force
"Eco-Barrel Cover" can reduce heat dissipation into the factory, thus contributing to reduced factory air conditioning costs and improved workplace environment, especially in summer.
(However, in the case of a factory without air conditioning, air conditioning costs cannot be reduced.)Assumptions for estimation
☆Machine | 1050em II-160 |
☆Product weight | 1KG |
☆Resin | PP |
☆Molding cycle time | 63sec |
Item | Heater power/wh/shot | Heater power/wh/shot |
---|---|---|
Standard cover | 211 | 496 |
Eco Barrel Cover | 148 | 433 |
Reduction Effect | 30% Reduction | 12% Reduction |
DIEPREST
The precision mold open/close control operation DIEPREST reduces mold clamping force through low-pressure molding using one of the DIEPREST functions, thereby downsizing the required molding machine and reducing the machine's operating energy.
DIEPREST molding: Reduction of mold clamping force
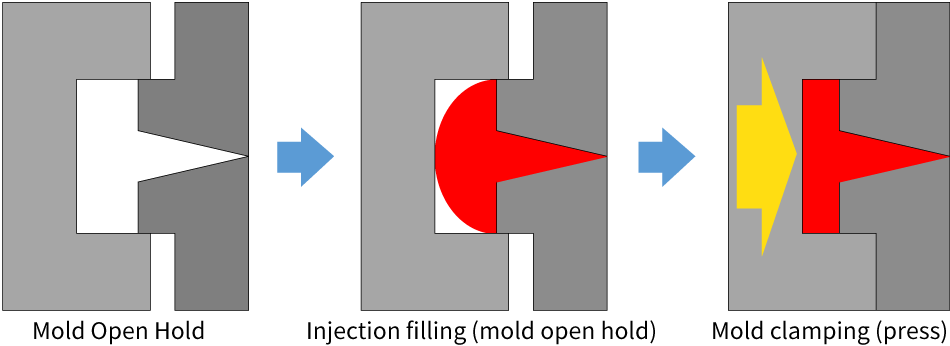
Size of Flat plate |
Product Dimensions H x W (mm) |
Required clamping force (tonf) | |
Normal molding | DIEPREST molding | ||
32 inch | 410 x 720 | 1330~ | 740 |
40 inch | 520 x 920 | 2150~ | 1200 |
46 inch | 590 x 1110 | 2900~ | 1650 |
52 inch | 670 x 1170 | 3500~ | 2000 |
(Family mold molding)
SCS Molding (Sequential Cavity Separation)
This is UBE Machinery's control technology for efficiently molding multiple product groups on a single molding machine.SCS molding realizes energy savings by consolidating molding machines and auxiliary equipment and reducing the number of machines in operation.

Ultra-high mixing, dispersion screw
Ultra-high mixing, dispersing screw with color dispersing performance equivalent to that of mixing nozzles reduces energy loss in the setup and production processes.
- (1) Reduction of plasticizing power by lowering back pressure and shortening measuring time
- (2) Reduction of injection filling energy loss
- (3) Shorter setup time and energy loss by reducing the number of purging times during setup
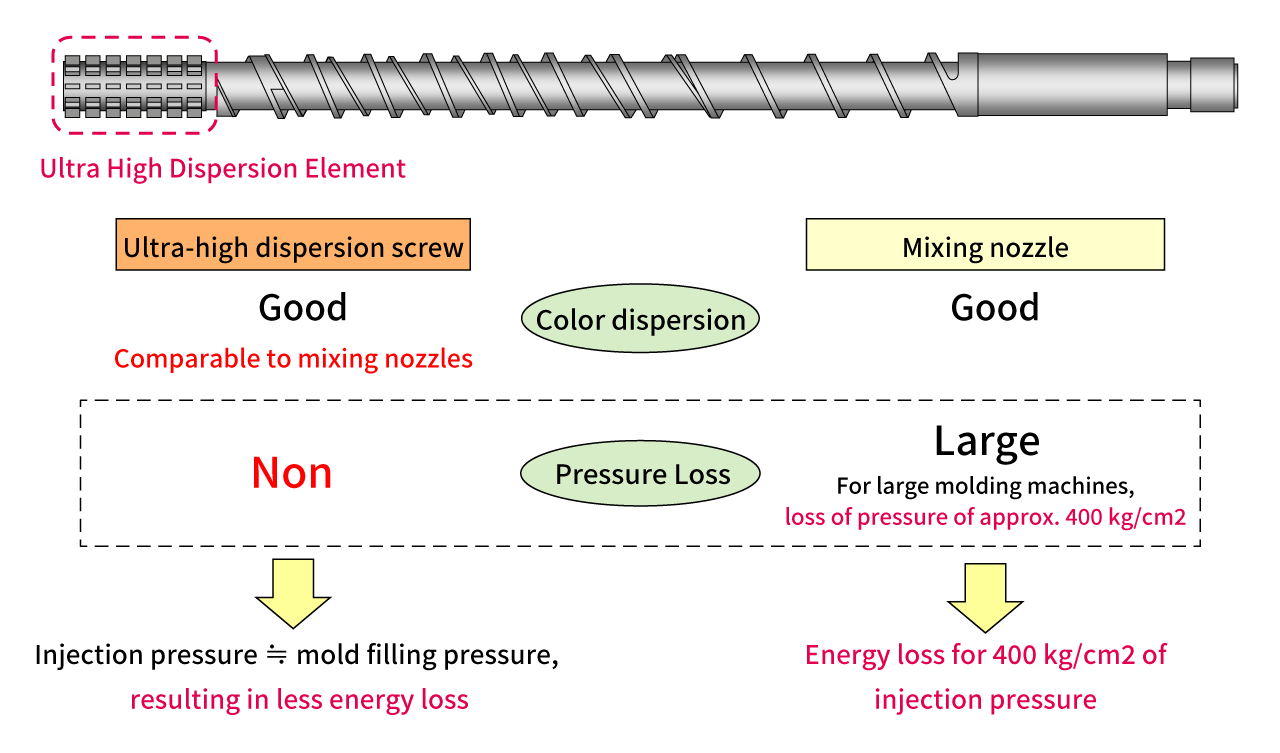
Power regeneration system
The braking energy of the drive motor used for mold opening/closing, plasticizing, and injection during deceleration is regenerated to the molding machine power supply, thereby reducing the drive energy loss of the molding machine.
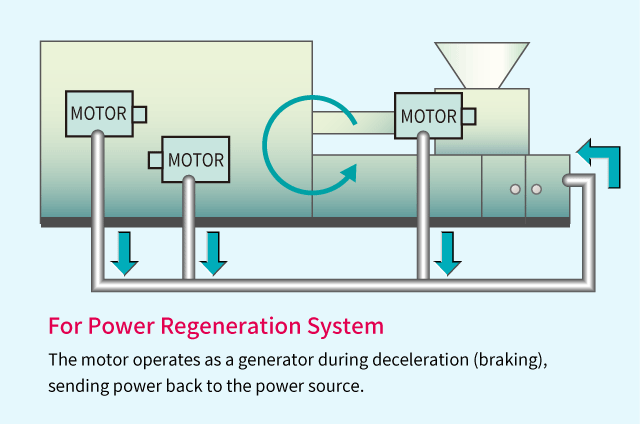
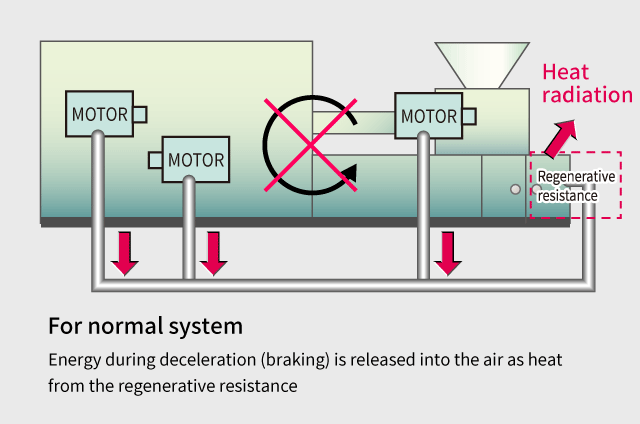
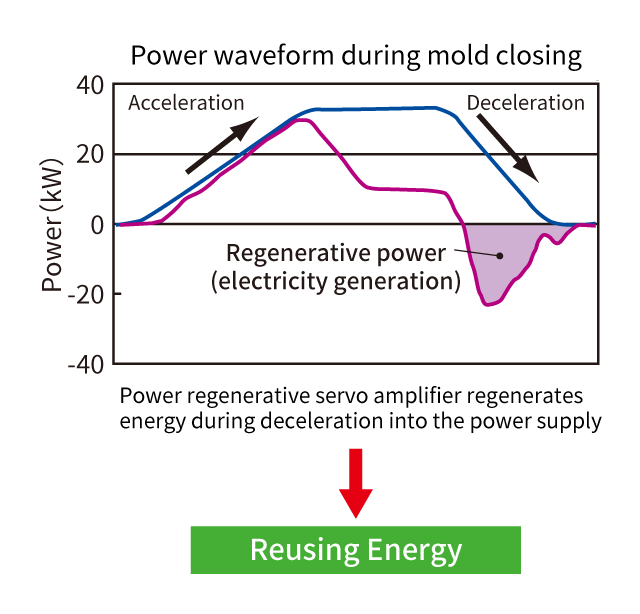
Further Energy Savings in Servo-Hydraulic Injection Molding Machine
Further Energy Savings in Servo-Hydraulic Injection Molding Machines
MMX Series
Equipped with "Energy-Saving Pump Control System" that contributes to carbon neutrality
UBE Machinery's MMX series servo-hydraulic injection molding machines employ UBE's unique "energy-saving pump control system," which is different from conventional servo-hydraulic machines. The MMX series achieves both reduced energy consumption and powerful continuous molding operation, thereby reducing customers' production costs and improving productivity. The hydraulic pump control system, which is driven only when operation is required, significantly reduces power consumption compared to conventional hydraulic machines, contributing to carbon neutrality.
“Energy-saving pump control system” (servo-driven pump system)
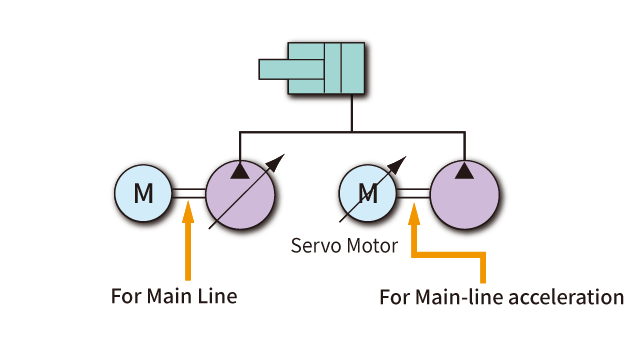
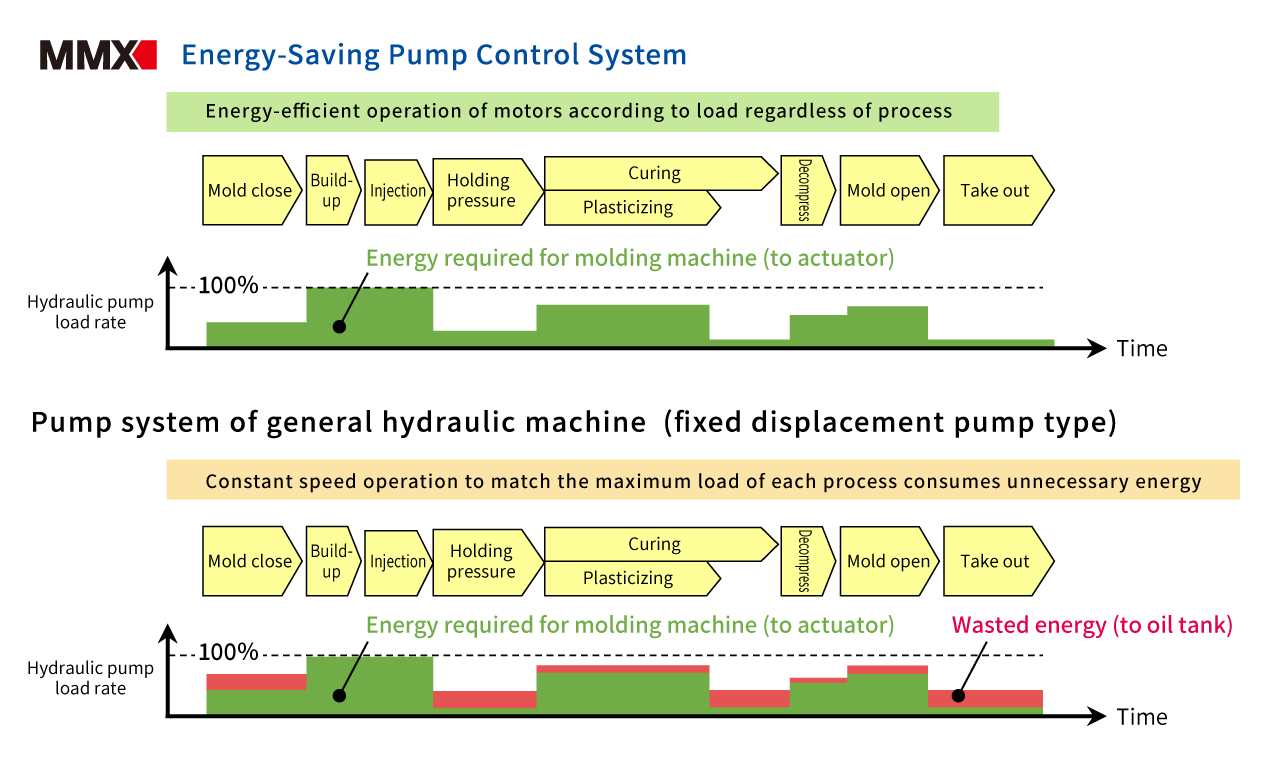
Injection Molding Machines/After-Sales Service
Proposal of energy saving improvement cycle
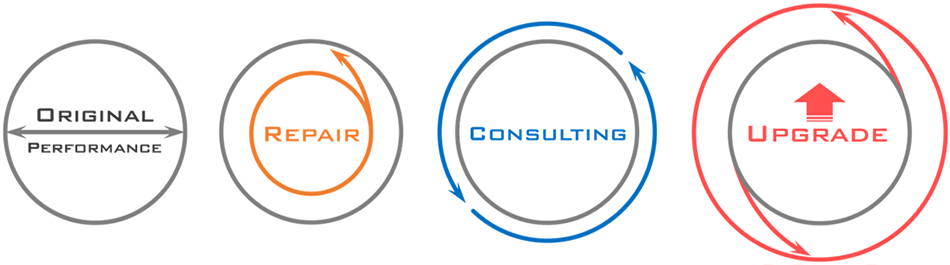
UBE Machinery offers a variety of upgrade and modification menus to improve the energy-saving performance of our injection molding machines that have been used by our customers for many years and contribute to carbon neutrality. Based on the results of power consumption measurement and analysis, we will identify items that can save energy and propose improvement items.
Power Consumption Measurement
We measure and analyze the power consumption of our injection molding machines used by our customers, and this is effective in identifying items where energy savings can be achieved.
Proposal of energy saving improvement cycle
Based on the results of power consumption measurement, it is effective to identify processes that consume a large amount of power and review the molding conditions to improve the process.
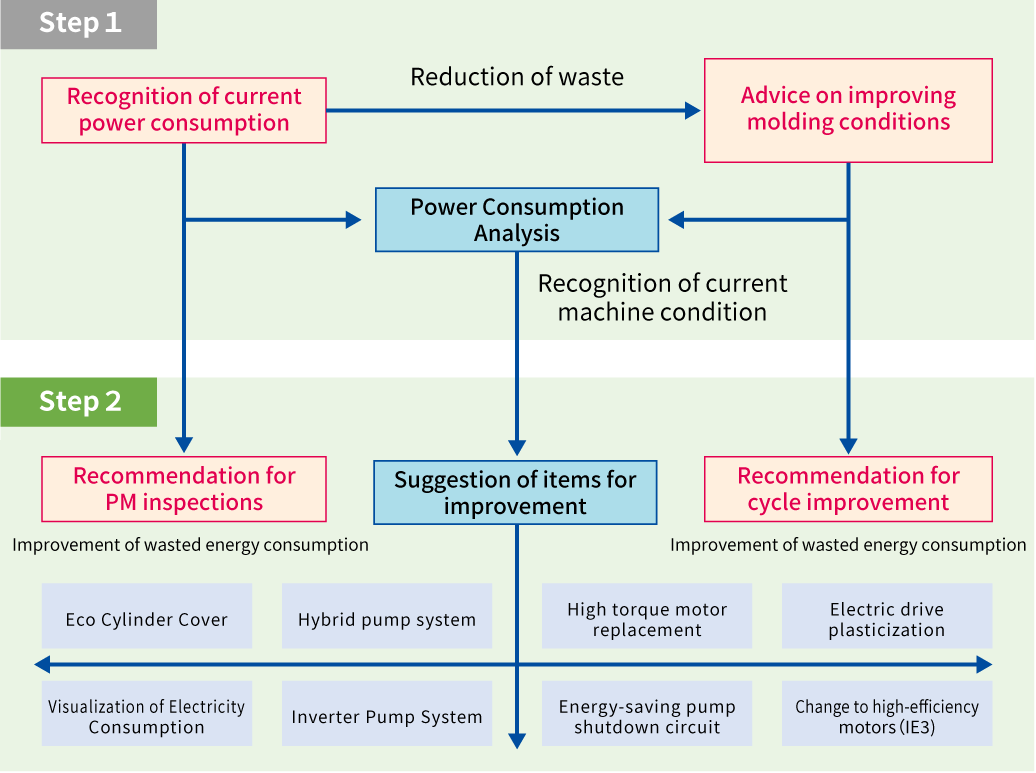